Oil seals, often referred to as rotary shaft seals, are crucial components in maintaining the efficiency and longevity of machinery. The keyword 10 63 oil seal denotes a specific type of oil seal, with the numbers often representing dimensions critical for fitment in machinery applications. This article delves into the significance of selecting the right oil seal, exploring its specifications, applications, and benefits, ensuring an enhanced understanding for both novices and seasoned mechanical engineers.
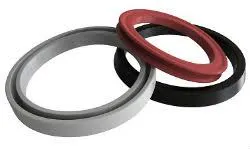
Oil seals play an integral role in preventing lubricants from leaking out of mechanisms and stopping harmful contaminants from seeping in. When searching for an oil seal such as 10 63 oil seal, it’s essential to grasp the numerical specifications that dictate its suitability for certain machinery. The numbers 10 and 63 typically refer to dimensions in millimeters the inner diameter (ID), and outer diameter (OD) of the seal, respectively. This specification ensures that users select a seal that fits precisely within the designated shaft or bore, a critical factor for optimal performance.
A 10 63 oil seal is often found in automotive, manufacturing, and industrial equipment due to its standard size, suitable for a wide range of applications. Machines such as pumps, gearboxes, and heavy-duty engines frequently utilize these seals to enhance operational efficiency. Their versatility extends to both rotary and reciprocating applications, highlighting the universality of this component.
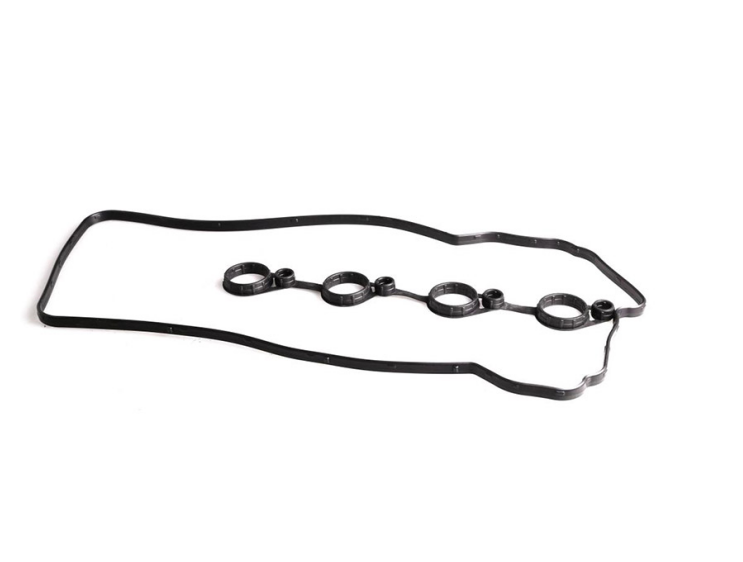
Selecting an oil seal with the appropriate material composition is equally critical. For the 10 63 oil seal, materials like nitrile rubber, fluoropolymer, or silicone are popular choices due to their temperature resistance, durability, and compatibility with different types of lubricants. Each material offers distinct advantages; for instance, nitrile rubber boasts excellent resistance to wear and is suitable for moderate temperatures, while fluoropolymer can withstand more extreme temperatures and chemical environments. Understanding these properties ensures that machinery operates reliably under various conditions, reducing maintenance costs and downtime.
10 63 oil seal
Beyond dimensions and materials, oil seal design features, including the sealing lip and spring mechanisms, enhance their performance. The inclusion of a garter spring in a 10 63 oil seal aids in maintaining consistent pressure on the rotating shaft, ensuring an effective seal even under fluctuating pressure and temperature conditions. Additionally, the sealing lip functions as a barrier, preventing fluid escape and ingress of contaminants, crucial for maintaining the integrity of lubricants that keep machinery running smoothly.
A well-chosen 10 63 oil seal not only prolongs machinery life but also contributes to energy efficiency. By preventing leakage, these seals mitigate the risk of environmental contamination and minimize the loss of lubricants, underscoring their eco-friendly credentials. Furthermore, they play a critical role in ensuring safety, as improper sealing can lead to mechanical failures that pose hazards to equipment operators.
For engineers and technicians, understanding the importance of precision in selecting oil seals like the 10 63 model elevates their capability to maintain and enhance machinery performance. It's not merely about fitting components but ensuring compatibility with operational environments and demands. Successful mechanical systems hinge on this attention to detail, where each component's role is optimized for the rigors of its application.
In conclusion, when optimizing for success in machinery maintenance and operations, the importance of selecting the right 10 63 oil seal cannot be understated. Its dimensions, material, and design intricacies determine its effectiveness in varied applications. By comprehensively understanding these facets, professionals can guarantee the reliability and efficiency of their equipment, reflecting the Experience, Expertise, Authoritativeness, and Trustworthiness in their fieldwork and design strategies. Embracing such technical precision enhances operational integrity, ensuring consistency and safety across all mechanical applications.