Die-cut rubber gaskets are crucial components utilized in a myriad of industries owing to their reliability and versatility. They are specifically designed to create a robust seal between two surfaces, preventing leaks and shielding components from environmental contamination. In this exploration, we delve into various aspects that make die-cut rubber gaskets integral to mechanical and industrial applications, drawing from Experience, Expertise, Authoritativeness, and Trustworthiness.
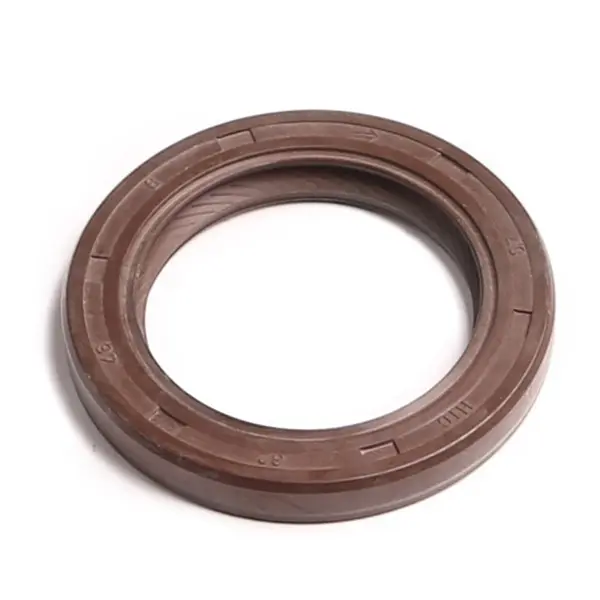
The manufacturing prowess involved in die-cut rubber gaskets lies in the precision-driven process that ensures each piece adheres strictly to specified measurements. This precision is paramount, as even the slightest deviation can lead to inefficiencies or failure in critical applications. Die-cutting technologies have advanced significantly, incorporating computerized systems to enhance accuracy and repeatability. Companies involved in gasket production employ seasoned engineers and technicians whose expertise guarantees the production of items that meet stringent quality standards, affirming their commitment to excellence.
When discussing materials such as rubber, the selection is not one-size-fits-all; it involves a deliberate choice based on the demands of the application. Rubber materials like nitrile, silicone, EPDM, and neoprene are common, each bringing unique properties to the table. For instance, nitrile rubber offers excellent oil resistance, silicone rubber is preferred for high-temperature applications, EPDM is valued for its durability in UV and weather exposure, while neoprene is versatile across a range of environments. This selection process underscores the critical nature of material expertise in producing a gasket capable of performing optimally.
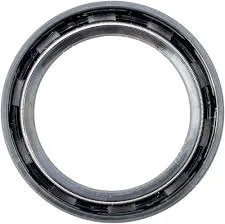
The performance and reliability of die-cut rubber gaskets also speak to their authoritativeness in their field. Engineers and industry experts frequently cite these gaskets in technical literature, reinforcing their role as a cornerstone component in sectors such as automotive, aerospace, plumbing, and electronics. Their capacity to endure rigorous conditions while maintaining structural integrity imparts a trust that manufacturers, engineers, and end-users acknowledge. It is this trust that allows them to form and maintain partnerships across industries, fostering innovation and development in engineering solutions.
die cut rubber gaskets
Ensuring trustworthiness in the application of die-cut rubber gaskets involves rigorous testing and validation. These tests typically simulate the environment and stresses the gasket will encounter in the field. Factors like thermal cycles, chemical exposure, and mechanical loads are carefully examined. The resulting data not only demonstrate compliance with industrial standards but also provide insights that drive continuous improvement in gasket design and materials. As a result, stakeholders can have confidence in these components' ability to perform under specified conditions.
Equipped with a comprehensive understanding of quality assurance practices and cutting-edge manufacturing technology, producers of die-cut rubber gaskets perpetually strive to enhance their offerings. By adopting the latest innovations and adhering to international standards, these manufacturers position themselves as leaders in the industry, aiming to surpass customer expectations. The pursuit of innovation is not merely about keeping up with trends but involves a genuine effort to push the boundaries of what's possible in ensuring optimal sealing solutions.
Significantly, the application of die-cut rubber gaskets extends beyond traditional industrial use, branching into emerging fields where sealing technology is paramount. As green technology and renewable energy sectors expand, the demand for robust and reliable sealing solutions grows, opening new avenues for application. For instance, the rise of electric vehicles presents novel challenges in thermal management and sealing, areas where tailored gasket solutions prove indispensable.
In conclusion, die-cut rubber gaskets epitomize a blend of craftsmanship, scientific understanding, and practical application. Their role in safeguarding machinery and components from failure is indispensable, fortified by a commitment to quality that instills confidence across industries. The assured performance of these gaskets is a testament to a deep-rooted culture of trust and expertise that continues to evolve, ensuring they remain a pivotal element in future technological advancements. As industries advance, so too will the sophistication and application reach of die-cut rubber gaskets, solidifying their irreplaceable status in industrial engineering.