Oil seals, often understated in their significance, serve as a silent sentinel in a myriad of mechanical systems. The 12x22x7 oil seal, despite seeming diminutive, plays a crucial role in maintaining the integrity and efficiency of engines and machinery. Renowned for its precise dimensions, this oil seal ensures that lubricants are efficiently contained while preventing contamination from external elements.
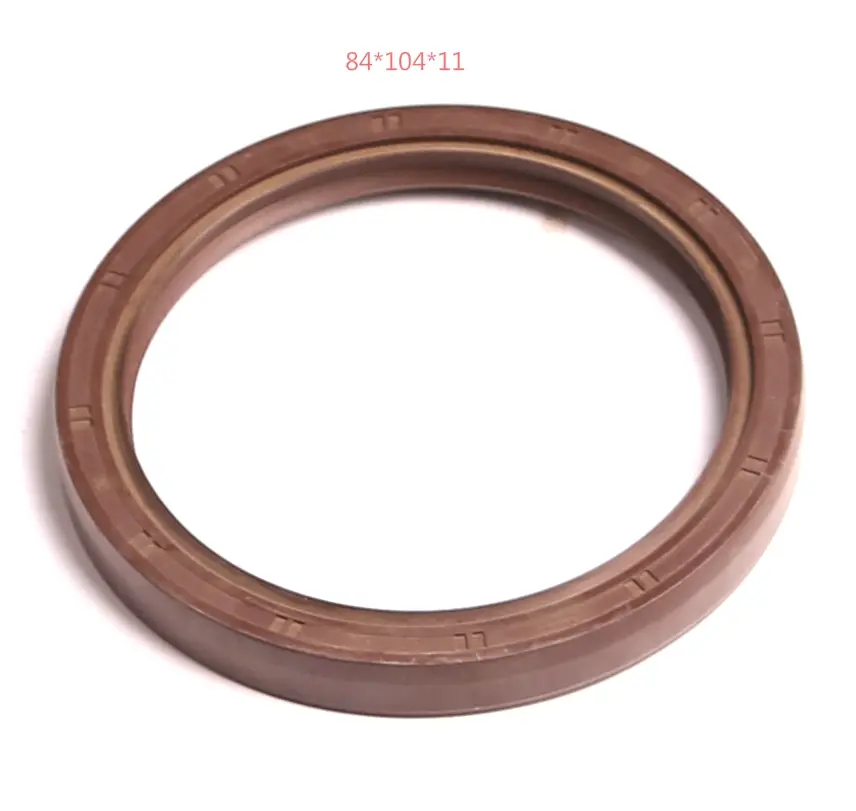
The essence of an oil seal lies in its ability to differentiate environments. With its expertly engineered structure, the 12x22x7 oil seal offers a robust barrier that effortlessly separates oil from the external surroundings. In doing so, it upholds the efficiency and longevity of the machinery it is utilized in, ensuring that components operate under optimal conditions without succumbing to premature wear or damage.
When selecting an oil seal, dimension specification is critical.
The 12x22x7 designation refers to its internal diameter, outside diameter, and width, respectively. This precision ensures that the seal will fit snugly between the rotating shaft and stationary housing, ruling out any potential for leakage—a vital attribute in maintaining mechanical efficiency and reducing downtimes.
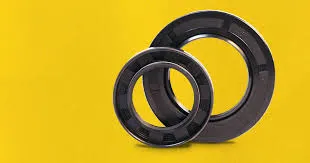
From a material perspective, oil seals are typically crafted from resilient components like nitrile rubber, silicone, or fluoroelastomers, each possessing unique resistances to temperature variations and chemical exposure. The choice of material for a 12x22x7 oil seal should align with the operational environment in question to maximize the seal’s lifespan and performance.
Installation of the 12x22x7 oil seal is a task that, though straightforward, demands attention to detail. Ensuring a clean work environment prevents contamination. Proper lubrication of the seal facilitates smoother installation and minimizes the risk of damage. Applying uniform pressure when embedding the seal avoids deformation, which might compromise its sealing capability.
12x22x7 oil seal
Real-world applications of 12x22x7 oil seals span across various industries. In automotive engineering, they are pivotal in axles and crankshafts, protecting against transmission fluid leakage. In industrial machinery, they ensure the stability of gearboxes and pumps, thus enhancing productivity. Their role in preventing environmental contamination cannot be understated, especially in sectors where cleanliness is paramount.
Manufacturers constantly strive to improve oil seal technology by innovating advanced composites and production techniques. The emphasis is increasingly on developing seals with higher heat tolerance, better chemical resistance, and enhanced wear properties, paving the way for sustainable solutions that meet modern engineering challenges.
In this landscape, the role of expertise and reliable sourcing cannot be overstressed. Engaging with suppliers who have industry credibility ensures that the quality and specifications of the oil seals are upheld. For businesses, sourcing from established entities not only enhances reliability but also optimizes operational economics through prolonged equipment lifespan and reduced maintenance costs.
To conclude, the 12x22x7 oil seal, while seemingly insignificant in size, is a cornerstone of mechanical reliability and efficiency. Its expert design and promising performance ensure the sustenance of machinery across various domains. Commitment to quality, expertise in installation, and adaptation to evolving technological avenues are essential in maximizing the potential of this crucial component. For organizations and individuals alike, harnessing the power of precision-engineered oil seals translates to tangible benefits in operational excellence and financial prudence.