Understanding the intricacies of selecting the right oil seal for your machinery can significantly impact the performance and longevity of the equipment. One specific size that demands attention is the 12x22x7 oil seal. This article delves into why this particular specification might be suitable for your needs and explores its application, benefits, and installation expertise.
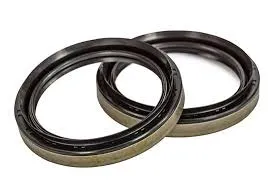
The 12x22x7 oil seal represents a crucial component in many mechanical systems designed to keep lubrication fluid in and prevent contaminants from entering. When choosing this specific size, understanding its applications is vital. Commonly utilized in automotive, agricultural machinery and various industrial equipment, the 12x22x7 oil seal is fabricated to fit specific shaft dimensions, ensuring optimal performance.
One cannot underestimate the importance of material selection in the construction of a 12x22x7 oil seal. These seals are typically made from high-quality rubber materials such as Nitrile (NBR), which provides excellent resistance to oils, fuels, and other chemicals. Depending on the operational environment, other materials like Fluoroelastomer (FKM) or silicone might be preferred due to their superior temperature resistance and chemical stability.
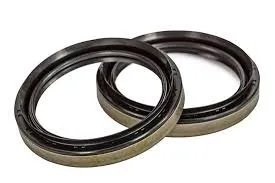
Incorporating a 12x22x7 oil seal into your machinery requires expertise that goes beyond mere installation. First and foremost, it's crucial to evaluate the seal size accurately to ensure a perfect fit. Accurate measurements of the shaft and housing—12mm shaft diameter, 22mm housing bore, and a 7mm width—are essential to avoid seal failure. It is equally important to consider the speed and pressure conditions under which the machinery operates. The seal needs to withstand the specific rotational speeds and pressures of the application to prevent premature wear and tear.
The benefits of using a 12x22x7 oil seal in machinery are manifold. Efficiently retaining lubricants prevents costly breakdowns and maintenance, ensuring a reduction in downtime and longevity in machinery life. Additionally, these seals help maintain environmental cleanliness by preventing leaks of hazardous fluids, aligning operations with eco-friendly standards.
12x22x7 oil seal
Despite its seemingly simple function, installation of the 12x22x7 oil seal requires attention to detail.
Expertise in proper handling and fitting ensures the seal performs optimally. During installation, surfaces should be clean and free of debris to prevent contamination. Using appropriate tools to press the seal into place evenly without distortion ensures a tight fit. Lubricating the seal lip can also facilitate a smooth installation, reducing the risk of tearing or misplacement.
Once the 12x22x7 oil seal is installed, regular maintenance checks should be part of an ongoing operational protocol. Regular inspections for wear or damage can preemptively address issues before they escalate, further cementing the role of these seals in predictive maintenance strategies.
Authoritative input from industry veterans underscores the importance of sourcing oil seals from reputable manufacturers, ensuring quality and reliability. Trusted brands often provide comprehensive data sheets with technical specifications and installation guides, guiding users through optimal usage scenarios.
In an era where precision and reliability are key competitive differentiators, selecting the right oil seal size and material is an investment in performance and efficiency. The 12x22x7 oil seal is a critical component for systems requiring tight sealing capabilities, offering peace of mind with its robust performance.
Ultimately, trusting in the right oil seal involves more than just purchasing the correct size; it encompasses a commitment to expertise in selection, installation, and maintenance. By adhering to these principles, you not only enhance equipment reliability but also contribute to the sustainable and efficient operation of your mechanical systems.