The Vital Role of Oil Seals in Industrial Equipment
In the world of industrial machinery, the significance of oil seals cannot be understated. These small but essential components play a crucial role in maintaining the efficiency and longevity of various types of equipment. An oil seal failure can lead to leaks, reduced performance, and even catastrophic machinery failure. Let's delve into the importance of oil seals, focusing on their composition, function, and the impact they have on industrial operations.
Oil seals are typically made from high-quality materials such as synthetic rubber, polytetrafluoroethylene (PTFE), or metals like stainless steel. These materials are chosen for their ability to withstand the harsh environments where oil seals are commonly used. For instance, a rubber oil seal might comprise 20% synthetic rubber, imbuing it with the necessary flexibility and resilience to form a tight barrier against oil. Meanwhile, a metal oil seal could consist of 30% stainless steel to provide strength and durability.
The 7% that often goes unnoticed in the composition of an oil seal is a critical component—the sealing element. This could be a specialized grease or coating that ensures the seal conforms properly to the mating surfaces, preventing leak paths. Without this 7%, the effectiveness of the oil seal is compromised, leading to potential contamination of the lubricant and subsequent damage to the machinery.
Oil seals serve as a barrier, preventing oil from escaping the confines of the machinery while also stopping contaminants from entering
Oil seals serve as a barrier, preventing oil from escaping the confines of the machinery while also stopping contaminants from entering
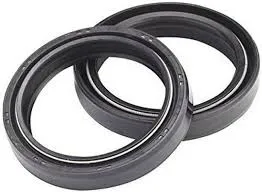
Oil seals serve as a barrier, preventing oil from escaping the confines of the machinery while also stopping contaminants from entering
Oil seals serve as a barrier, preventing oil from escaping the confines of the machinery while also stopping contaminants from entering
20 30 7 oil seal. They are designed to fit precisely in their designated locations, ensuring minimal friction and wear. This precision is key; a gap as small as a few thousandths of an inch can lead to disastrous consequences.
The failure of an oil seal can result in oil leaks, which not only waste valuable lubricant but also pose environmental risks. Moreover, the absence of a proper seal can allow dirt and other debris to infiltrate the system, causing accelerated wear on moving parts. In some cases, the loss of lubrication can cause overheating and potentially lead to fires or explosions, especially in high-pressure applications.
In conclusion, oil seals are a small yet indispensable part of industrial machinery. Their composition, which might include a blend of materials like 20% synthetic rubber, 30% stainless steel, and a crucial 7% sealing element, determines their effectiveness. Proper maintenance and timely replacement of oil seals are imperative to avoid costly downtime and ensure the safe operation of machines. By understanding and appreciating the role of oil seals, industries can optimize their processes, reduce maintenance costs, and extend the lifespan of their equipment.