Navigating the world of industrial components, the 70x90x10 oil seal emerges as an essential element, integral to ensuring machinery operates smoothly and efficiently. This particular seal, defined by its dimensions of 70mm inner diameter, 90mm outer diameter, and 10mm width, plays a critical role in the functionality and longevity of mechanical systems. Understanding its importance requires diving deep into its experience-based benefits, technical expertise, authoritative applications, and the trust it commands among engineers and technicians.
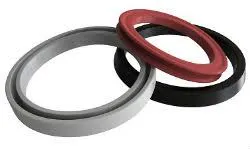
The 70x90x10 oil seal’s main function is to prevent the leakage of lubricants and the ingress of contaminants. This is paramount in maintaining the efficiency and reliability of rotating shafts and bearing systems. In machinery, every component must operate harmoniously, and this seal ensures that by serving as a barrier that protects internal environments from external contaminants like dust, dirt, and moisture. Its design is tailored to withstand high-pressure environments, commonly found in automotive gearboxes, industrial pumps, and hydraulic systems.
Expertise in using the 70x90x10 oil seal is derived from a comprehensive understanding of its material composition. Typically, these seals are made from high-quality synthetic rubber materials, such as Nitrile, Viton, or Silicone, each selected based on specific operational needs and resistance requirements. Nitrile is often chosen for its versatile temperature range and resistance to oil and fuel, making it ideal for most standard applications. Viton, known for its excellent heat resistance and chemical stability, is used in more corrosive environments. Meanwhile, Silicone seals are favored for their flexibility and longevity in extreme temperatures. This knowledge guides technicians in selecting the appropriate seal for their machinery, ensuring optimal performance and durability.

70x90x10 oil seal
Authoritativeness of the 70x90x10 oil seal is further established through its widespread industry applications. Companies operating heavy machinery rely on these seals to enhance equipment reliability. Industries such as automotive, aerospace, manufacturing, and marine have long trusted this seal design for its proven track record. In automotive engineering, for instance, these seals are crucial in transmissions and engine systems, where failure could lead to significant operational disruptions and maintenance costs.
The use of proper seals like the 70x90x10 can prevent unforeseen breakdowns, preserving machinery integrity and reducing downtime.
Trustworthiness is built over time through rigorous testing and compliance with industry standards. Reputable manufacturers ensure these seals undergo stringent quality assurance processes, adhering to ISO certifications and other regulatory benchmarks. This not only affirms the product’s reliability but also bolsters client confidence. The ongoing feedback loop from real-world applications provides continual product refinement, further strengthening trust in the product’s capability to meet demanding requirements.
In conclusion, the 70x90x10 oil seal is not just a simple component; it is a critical player in the seamless operation of mechanical systems. Its role in preventing leakage and contamination, combined with its robust material selection and compliance with industry standards, makes it indispensable. Both experts and novices in mechanical engineering recognize the value it provides in extending machinery lifespan and enhancing performance. As industries evolve, so too do the technologies and materials used in oil seals, but the fundamental principles of reliability and protection remain at the heart of their design. Understanding and implementing the right oil seal effectively continues to be a cornerstone of industrial maintenance and operation efficiency.