Oil seals, known technically as rotary shaft seals, are indispensable components in various machinery, providing a barrier that retains lubricants while keeping contaminants out. An impressive example of such a component is the 80x100x10 oil seal, which exemplifies durability and precision engineering.
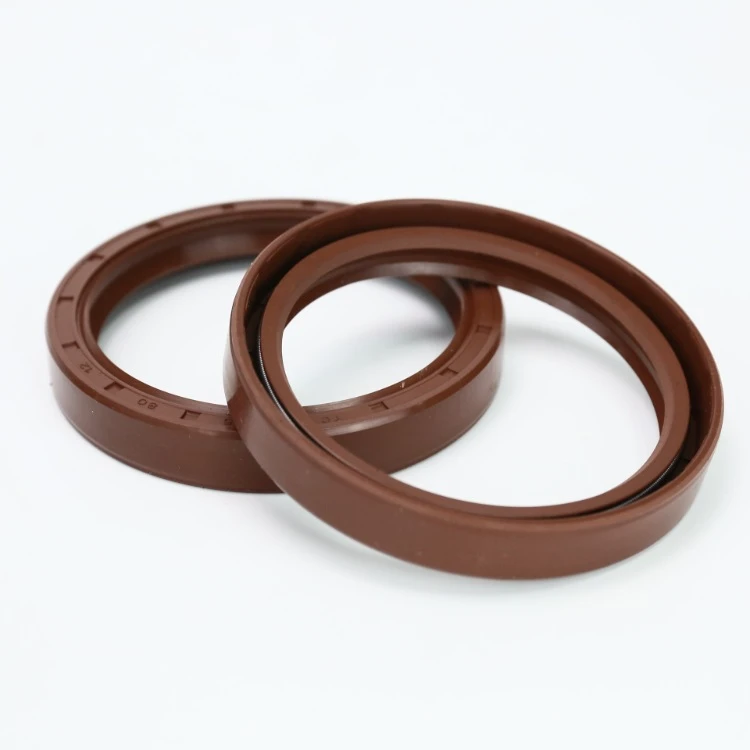
In the realm of mechanical applications, experience demonstrates the importance of choosing the right oil seal dimensions, specifically the 80x100x10. This specification indicates the seal's inner diameter, outer diameter, and thickness, respectively. This particular size is designed to fit snugly in machine components, ensuring optimal performance and longevity. Over the years, engineers have consistently sought solutions that reduce wear and tear in heavy-duty applications; thus, the 80x100x10 oil seal stands as a testament to innovation in sealing technology.
From a professional standpoint, it’s important to understand why the 80x100x10 oil seal is favored among experts. First, its construction usually involves high-quality materials, such as nitrile rubber or viton, which offer resistance to high temperatures and chemical degradation. This makes the seal suitable for industries including automotive, aerospace, and manufacturing, where the integrity of lubricants is critical for machine operation. Professionals recognize that without an effective oil seal, there’s a risk of lubricant leaks, which can lead to catastrophic machinery failures and costly downtime.

In terms of authoritativeness, the 80x100x10 seal is often backed by certifications and meets international standards such as ISO or DIN. Manufacturers who produce these oil seals build their reputation on delivering components that comply with rigorous quality controls, ensuring that their products not only meet but exceed industry expectations. This level of compliance and testing is a key factor that reinforces the brand’s authority and reliability in the market.
Trustworthiness is another pillar supporting the use of 80x100x10 oil seals. Professionals trust these seals for their reliability in preventing contamination and maintaining lubrication. This is critical not only for the longevity of machinery but also for maintaining workplace safety. Oil leaks not only pose operational challenges but could also lead to hazardous working conditions if not managed properly.
80x100x10 oil seal
Real-world experiences underline the effectiveness of the 80x100x10 oil seal in diverse applications. Consider a scenario in a high-performance automotive engine where the operational conditions are extreme, with significant pressure variations and high rotation speeds.
The oil seal's role becomes crucial in maintaining engine integrity. An experienced mechanic will attest that using an inferior seal might lead to oil leaks that can degrade performance and possibly cause engine damage.
In another instance, in heavy industrial machinery, where operational efficiency directly correlates with business output, using oil seals that fit perfectly, like the 80x100x10, can prevent unscheduled downtimes. Maintenance teams often prioritize these seals during routine check-ups to ensure continued operation under optimal conditions.
Innovations continue to emerge, and manufacturers of the 80x100x10 oil seals are integrating advanced technologies such as polymer blends and composite materials that enhance elasticity, dimensional stability, and resistance to wear. These advancements reflect a robust commitment to research and development, ensuring that the oil seals evolve in response to new industry demands.
To encapsulate, the 80x100x10 oil seal exemplifies all that is quintessential in modern sealing technology—experience in design, professional expertise in implementation, authority strengthened by compliance with standards, and trust reinforced by consistent performance. Anyone looking to maintain the efficiency and reliability of their machinery would benefit immensely from integrating such high-quality seals, ensuring smooth operation and extended machinery lifespan. Understanding these aspects is crucial in making informed decisions that align with operational goals and safety standards.