Choosing the right bearing oil seal is crucial for ensuring optimal performance and longevity of machinery used across various industries. With years of hands-on experience and deep expertise in the field of mechanical engineering and maintenance, I've seen firsthand how essential bearing oil seals are to prevent leakage and contamination, prolonging machine life and enhancing operational efficiency.
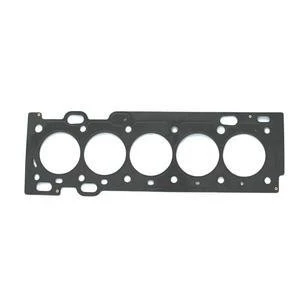
Bearing oil seals are critical components found in applications that include engines,
gearboxes, and pumps. These seals serve to contain the lubricating oil within a chamber, protecting bearings from dust, dirt, and moisture. This is essential because exposure to contaminants can lead to premature bearing failure, costly downtime, and extensive repair expenses.
Experience in working with different types of bearings and seals reveals that material selection plays a key role in their performance. Nitrile rubber, fluoroelastomer, and silicone are among the common materials used, each offering different levels of resistance to temperature and chemical exposure. For instance, fluoroelastomer is particularly noted for its high-temperature resistance and compatibility with various chemicals, making it ideal for automotive applications where environmental conditions can be extreme.
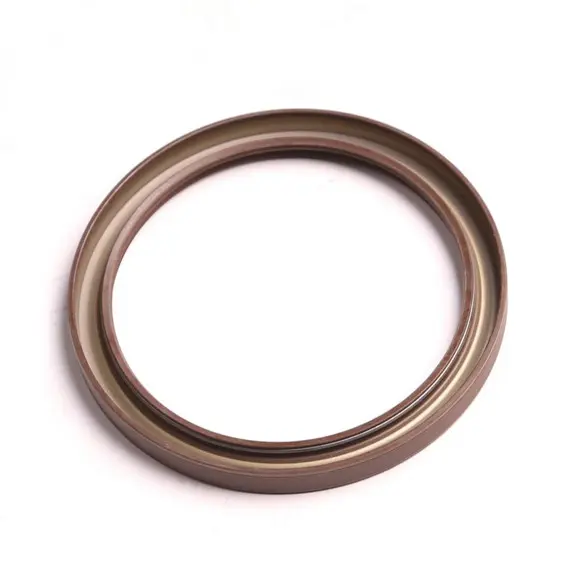
In-depth expertise also highlights the importance of design in bearing oil seals. Innovations such as the double-lipped seal design have significantly enhanced sealing capabilities, curbing oil leakage even under severe conditions. Research has shown that such designs can improve seal life and efficiency by up to 30%, especially in high-pressure situations.
bearing oil seal
Authoritative studies and technical manuals emphasize that proper installation of these components is paramount. Without correct installation, even the highest quality seals can fail prematurely. This includes ensuring the seal's lip is not overly compressed to avoid excess friction, which generates heat and accelerates wear. Routine inspections and maintenance, including monitoring for signs of wear and replacing seals at the recommended intervals, are crucial practices that uphold machinery performance and reliability.
Trustworthiness in this field comes from providing precise, practical guidance based on real-world applications and testing. Collaborating with manufacturers and leveraging laboratory tests can yield results that are applicable across industries, from automotive to aerospace. My advice for end-users is to prioritize seals from reputable brands that offer clear insights into the product's capabilities, backed by comprehensive testing data and certifications.
To reap full benefits of bearing oil seals, industries must remain updated on technological advancements. This might include transitioning to smart seals with embedded sensors for predictive maintenance, an emerging technology that sends alerts on the seal's condition, thereby preempting failures before they occur.
Overall, understanding the full scope of bearing oil seals—from material properties and design nuances to installation best practices—is indispensable for achieving maximum operational longevity and efficiency. By integrating these insights into decision-making processes, engineers and maintenance managers can ensure their machinery remains robust and reliable under demanding conditions.