Custom oil seals, pivotal components in industrial machinery, cater to diverse applications, ensuring equipment longevity and optimal performance. Each seal, meticulously designed, prevents leakage and contamination, particularly in complex mechanical systems. Choosing the right custom oil seal enhances machine reliability, extends service life, and maximizes operational efficiency.
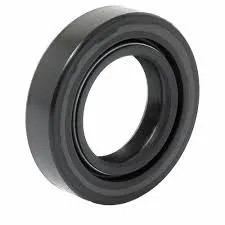
When selecting custom oil seals, one must consider material composition, which significantly impacts performance. Nitrile rubber, fluoroelastomer, silicone, and PTFE are popular materials used in oil seals, each exhibiting distinct properties suited to specific environments. For instance, nitrile rubber offers excellent resistance to oil and abrasion, making it ideal for automotive and industrial machinery applications. In contrast, fluoroelastomer is preferred in high-temperature settings due to its outstanding heat and chemical resistance.
Dimensional accuracy is another critical factor. Precise engineering of an oil seal ensures a perfect fit within mating surfaces, reducing the risk of oil leakage and mechanical failure. Manufacturers leverage advanced manufacturing technologies, including CNC machining and 3D modeling, to produce seals that meet stringent dimensional tolerances.
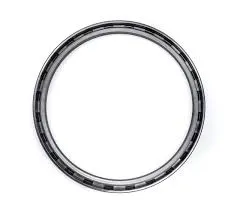
The application environment profoundly influences the choice of custom oil seals. In harsh or extreme conditions, such as high-pressure systems or corrosive environments, seals must withstand significant stressors. Utilizing advanced simulation and testing methodologies, experienced engineers can predict a seal's performance under various conditions, ensuring it meets operational demands.
An often overlooked aspect is the seal lip design, a crucial feature that affects the seal's functionality. Single lip, double lip, and triple lip designs serve different sealing purposes and environments. A double lip oil seal, for example, offers both primary sealing and additional protection against external contaminants, making it suitable for applications in dirty or abrasive environments.
custom oil seals
Custom oil seal manufacturers play a critical role in innovation, employing expertise and cutting-edge technologies to deliver high-performance sealing solutions. Collaboration with knowledgeable manufacturers provides clients access to the latest materials, designs, and engineering practices. Such partnerships not only yield superior products but also foster ongoing technical support, crucial during the product lifecycle.
As machinery evolves,
the demand for specialized sealing solutions intensifies. Custom oil seals are increasingly tailored to accommodate complex systems, including renewable energy equipment, advanced automotive systems, and aerospace applications. In these sectors, the importance of leak prevention and the capability to manage extreme pressures and temperatures cannot be overstated.
Credibility and trust in custom oil seal solutions are established through strict adherence to global standards and certifications, such as ISO and DIN. Compliance ensures that products meet international quality and safety standards, providing clients with assurance and confidence in their choice of sealing solutions.
Investing in well-designed custom oil seals reduces maintenance costs and downtime, drastically enhancing a business's bottom line. Efficient sealing solutions not only prolong machinery life but also contribute significantly to environmental conservation by minimizing oil leakage and spillage.
In conclusion, the expertise involved in creating custom oil seals underscores their significance in industrial applications. From material selection and dimensional precision to understanding application environments and maintaining global standards, each aspect reflects the expertise required. Partnering with authoritative manufacturers enhances trust and reliability, establishing custom oil seals as indispensable components in the quest for efficient and durable industrial solutions.