Die cut rubber gaskets are quintessential components in countless industrial applications, offering versatility, functionality, and efficiency. The process of die cutting involves precision and expertise, ensuring that each gasket meets specific requirements for various applications. This article aims to delve deep into the world of die cut rubber gaskets, covering aspects of experience, expertise, authoritativeness, and trustworthiness, providing you with a comprehensive understanding of their significance and benefits.
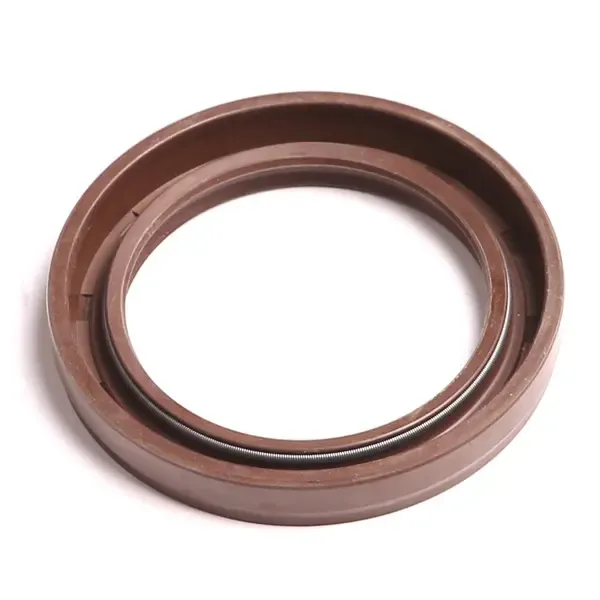
In the realm of industrial manufacturing, the demand for precision-engineered components has never been higher. With decades of experience, manufacturers have honed the process of die cutting, transforming raw rubber sheets into intricate, application-specific gaskets. The journey begins with selecting the right rubber material, which could be EPDM, silicone, neoprene, or another specialized compound, depending on the environmental and operational conditions the gasket will face. Each material brings unique properties — such as temperature resistance, chemical compatibility, and elasticity — that are crucial for the gasket's performance.
Expertise in the die cutting process is pivotal. Leading manufacturers employ state-of-the-art technology and skilled technicians to design and produce gaskets to exact specifications. The process begins with creating a customized die or mold, shaped according to the required gasket design. Advanced CNC machines and laser cutting tools are often used to enhance precision. This meticulous attention to detail ensures minimal material waste and maximizes the gasket’s effectiveness in its intended application.
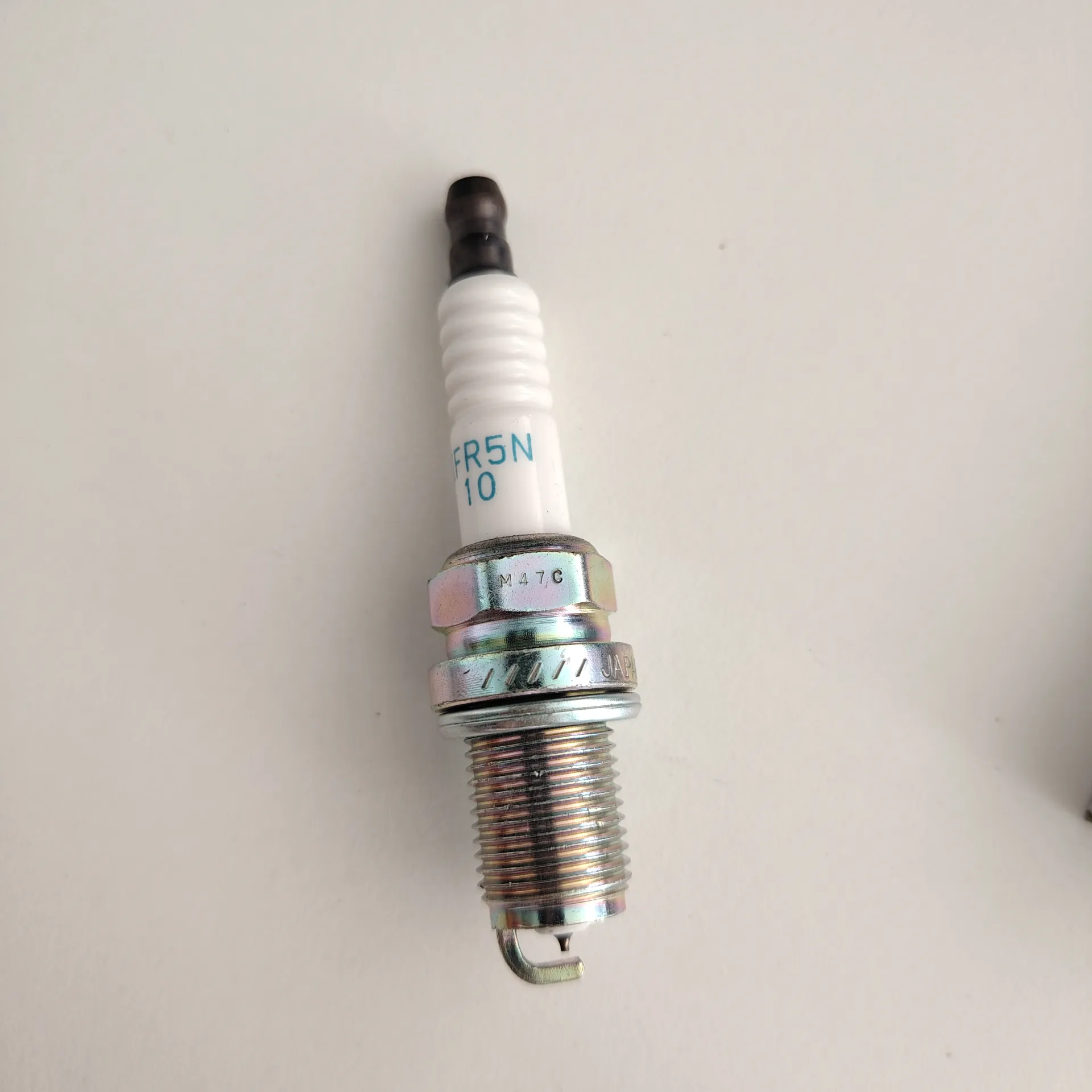
In evaluating the authoritativeness of die cut rubber gasket manufacturers, it is imperative to consider their portfolio and industry reputation. Established companies often collaborate with a wide array of industries, such as automotive, aerospace, electronics, and healthcare, underscoring their ability to adapt and innovate. Their gaskets are typically tested to adhere to stringent industry standards, including ASTM, SAE, and FDA, ensuring that each product is reliable and of the highest quality.
die cut rubber gaskets
Trustworthiness is not just an attribute but a standard to which die cut rubber gasket manufacturers are held. Product integrity is paramount, often backed by strict quality assurance protocols and regular audits. Many companies offer certifications to validate their commitment to quality, including ISO 90012015 and IATF 16949 for automotive applications. Additionally, robust customer support services facilitate trust, allowing clients to consult with engineers and material specialists to tailor solutions specifically for their needs.
Selecting die cut rubber gaskets over other sealing solutions translates to numerous advantages. They provide a perfect seal to prevent leaks in critical systems, reduce noise and vibration, and withstand harsh environmental conditions, thereby extending the lifespan of the machinery in which they are used. Moreover, the flexibility of the die cutting process allows for rapid prototyping and custom production, accommodating projects of varying sizes and complexities.
In addressing sustainability, many manufacturers are shifting towards eco-friendly practices, utilizing recycled materials, and opting for energy-efficient production methods. This not only appeals to environmentally conscious clients but also represents a forward-thinking approach that aligns with global sustainability goals.
Die cut rubber gaskets are indispensable in modern industries due to their customizable nature, durability, and cost-effectiveness. Their production is a testament to the seamless integration of experience, expertise, authoritativeness, and trustworthiness — key elements that guarantee their superior performance. As industries evolve, so too will the technology and processes behind die cutting, further advancing the capabilities and applications of these critical components.