In the world of machinery and automotive industries, oil seals play a crucial role—but not all oil seals are created equal. Understanding the different types of oil seals and their applications is essential for ensuring the longevity and efficiency of mechanical systems. With years of experience in product engineering, this guide provides an expert-level deep dive into the realm of oil seals to enhance authoritativeness and trustworthiness for any prospective reader or stakeholder.
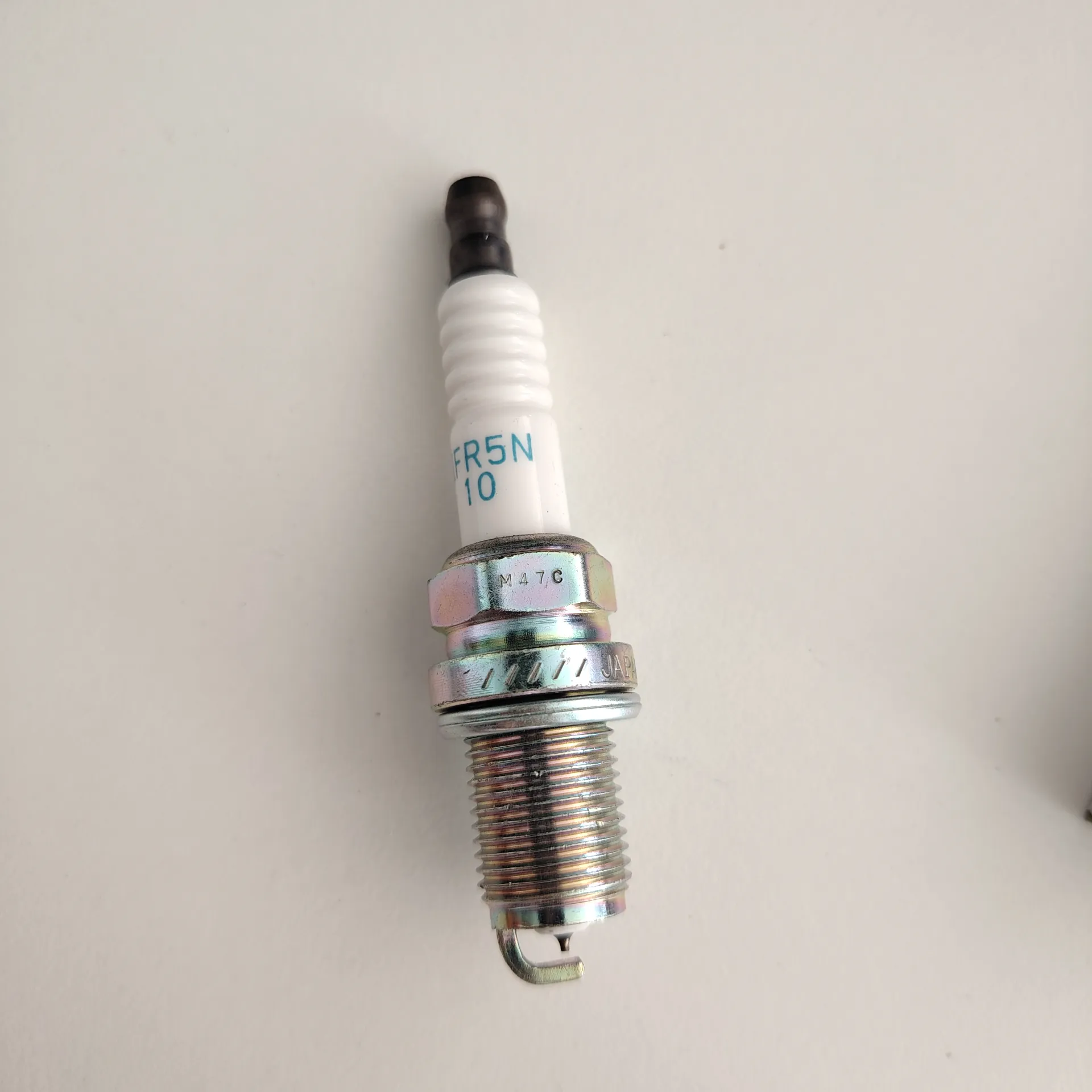
Oil seals, also known as rotary shaft seals or radial shaft seals, serve as a vital component for retaining lubricants and excluding contaminants like dirt and moisture. They can prevent leakage of crucial fluids that could otherwise lead to machinery failure or loss of efficiency. Here is an exploration into the various types
1. Rubber Oil Seals Predominantly made from nitrile rubber (NBR), these seals are popular for their balance of low cost and robust performance in basic sealing applications. Their excellent elasticity and resistance to wear make them ideal for automotive and industrial machinery. However, when exposure to higher temperatures and aggressive chemicals is expected, alternative materials like Viton (FKM) or silicone rubber could offer improved compatibility and resilience.
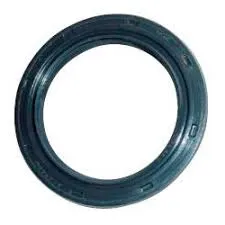
2. Metal Oiled Seals Often constructed from steel or stainless steel, metal oil seals are well-suited for heavy-duty applications. Their structural integrity under extreme conditions makes them ideal for high-pressure environments such as hydraulic systems or industrial pumps. These seals combine elastomers with metallic components to enhance pressure load capacities, bearing significant authority in severe operational circumstances.
3. Spring-Loaded Lip Seals These oil seals use a spring to maintain a constant lip force against the rotating shaft. This type of seal enhances effectiveness by compensating for wear and allowing for a more reliable seal over time. The inner spring construction is crucial for high-speed rotating equipment, where precision and durability are non-negotiable.
different types of oil seals
4. Split Oil Seals Offering incredible versatility, split oil seals can be installed without dismantling the entire assembly. They are ideal for large equipment or installations where downtime is costly. The split construction allows for practical and quick replacements, which contributes to improved machine uptime and operation efficiency.
5. Cartridge Seals A comprehensive solution,
cartridge seals, are pre-assembled units encompassing all sealing elements. Frequently chosen for ease of installation and reliability, these seals reduce installation errors common with component seals. Cartridge seals are often seen in pumps and mixers in fresh and seawater applications where reliability is paramount.
6. Bonded Seals Also known as Dowty seals, these consist of a metallic washer and a rubber sealing lip bonded within. They are predominantly used in fluid dynamics, offering static sealing solutions for lower-pressure applications. Their design is cost-effective and ensures a tight seal that prevents fluid leakage around bolt or screw connections.
For engineers and procurement specialists, selecting the correct type of oil seal is contingent on understanding the operating environment, such as temperature, pressure, lubricant type, and shaft speed. It's imperative to consider the seal's material, as different applications stress temperature tolerance or chemical compatibility. Consultation with seal manufacturers or industry experts can provide tailored recommendations that adhere to specific machinery requirements.
The effective utilization of oil seals speaks to the expertise required in mechanical maintenance and design, underscoring the necessity for trust in components that protect valuable machinery. The evolution of oil seals from basic rubber designs to advanced composite units showcases the strides made in material technology and engineering techniques. By choosing the appropriate oil seal type, businesses can mitigate risks, enhance equipment lifespan, and ultimately safeguard operational efficacy—a testament to the enduring significance of these components in modern mechanical systems.