Unlocking the Potential of Double Lip Oil Seals for Enhanced Machinery Performance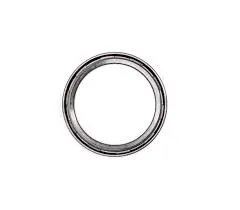
Double lip oil seals are indispensable components in the world of machinery and automotive applications. These seals play a critical role in maintaining system integrity by preventing fluid leaks and blocking contaminants, thus ensuring smooth operation and longevity of equipment. A deep dive into the functionality, application, and benefits of double lip oil seals highlights their significance in optimizing machinery performance.
The design of a double lip oil seal is pivotal to its effectiveness. Featuring two distinct lips—a primary lip that retains the lubricant and a secondary lip that keeps dirt and other contaminants out—these seals deliver enhanced protection compared to their single-lip counterparts. This dual-action capability allows machinery to operate seamlessly, minimizing wear and tear that often leads to costly repairs and downtime. Moreover, the secondary lip acts as an additional barrier, offering protection even if the primary lip experiences wear or damage, thereby extending the overall life of the component.
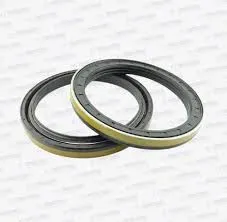
One of the most significant advantages of double lip oil seals is their versatility across various applications. Whether in automobile engines, industrial equipment, or hydraulic systems, these seals are adaptable to environments where reliability is paramount. They are engineered from materials such as nitrile rubber, fluoroelastomer, and silicone, providing options for different temperature ranges and chemical exposures. This adaptability ensures that they meet the rigorous demands of both high-speed and high-pressure applications, which are common in industrial settings.
double lip oil seal
Expertise in selecting the appropriate double lip oil seal is essential to realizing its full potential. Engineers and maintenance personnel must consider factors such as shaft speed, operating temperature, and environmental conditions when choosing the right seal for their specific application. The correct choice not only maximizes the seal's efficiency but also contributes to the overall performance of the machinery. Professional consultation with manufacturers or suppliers can provide insights into the best practices for installation and maintenance, ensuring that seals are fitted correctly and function optimally throughout their service life.
Authoritative sources and industry leaders underline the importance of regular inspection and maintenance of double lip oil seals. Routine checks can identify early signs of wear and potential failure, allowing for proactive measures to be taken before major issues arise. Lubrication is another critical aspect; the primary lip needs adequate lubrication to minimize friction and wear, which can be accomplished through the proper choice of grease or oil. Additionally, overcoming challenges such as shaft misalignment and pressure fluctuations is key to preventing undue stress on the seal, which can lead to premature failure.
Trustworthiness is a vital component when selecting both the product and the supplier. Reputable manufacturers provide detailed product specifications and performance data to ensure transparency and build confidence in their products. Investing in seals from trusted brands with proven track records ensures that machinery is equipped with reliable components, thus securing the investment and mitigating risks associated with equipment failure.
In summary, double lip oil seals are critical for protecting the integrity and efficiency of machinery across a multitude of sectors. Their unique design and versatility make them an essential component that, when selected and maintained correctly, provides exceptional performance and extends the lifespan of equipment. With expert guidance, regular maintenance, and trusted sourcing, these seals offer a robust solution to the challenges of fluid leakage and contamination, paving the way for improved operational reliability and lower maintenance costs. Embracing the advantages of double lip oil seals translates into tangible benefits, such as improved productivity and reduced downtime, making them a vital asset in the realm of modern machinery.