The double oil seal, an essential element in engineering and mechanical applications, plays a pivotal role in ensuring the longevity and efficiency of various machinery. Its importance cannot be understated, as it provides an additional layer of protection against contaminants and leakages that could otherwise lead to costly downtimes and repairs. In the realm of mechanical engineering, understanding the intricacies of double oil seals can enhance operational success.
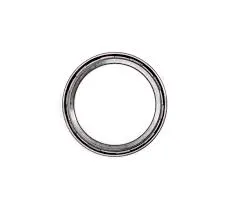
The primary function of a double oil seal is to prevent the ingress of dirt, dust, and other harmful particulates while simultaneously keeping essential lubricants from escaping. This dual capability is crucial in industries such as automotive, aerospace, and industrial manufacturing, where precision and reliability are non-negotiable. For instance, in automotive engines, double oil seals help maintain optimal oil levels, ensuring that engines run smoothly and efficiently without the risk of oil leaks that could cause extensive damage.
Specialized design features contribute to the effectiveness of double oil seals. Typically, these seals consist of two lips the primary lip, which maintains the separation of the lubricant from external contaminants, and the secondary lip, which provides an additional defense line. This dual-lip structure is engineered using advanced materials such as nitrile rubber, silicone, and fluorocarbon, each chosen for their specific properties of resistance to temperature variations, chemical exposure, and wear-and-tear. Selecting the right material composition is critical for achieving the desired performance in specific environmental conditions.
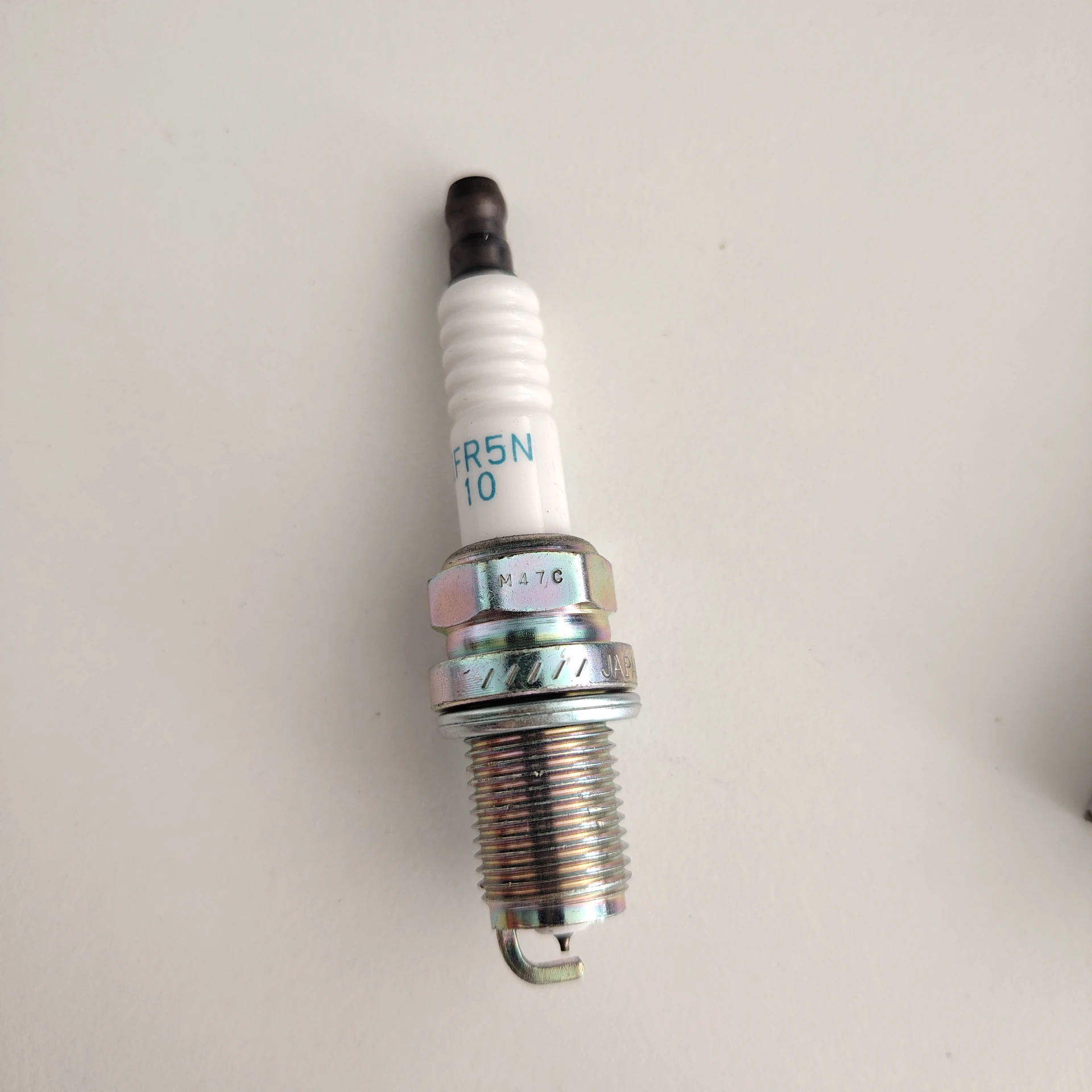
Expertise in the selection and installation of double oil seals is indispensable for maximizing their efficiency. A meticulous approach to the installation process can prevent premature seal failure, often caused by incorrect installation techniques. Expertise in dimensions, understanding shaft dynamics, and ensuring the seal housing is devoid of any abrasions or irregularities can significantly extend the lifespan of a double oil seal. Professionals often employ precision tools to align and insert each seal to prevent warping or damage during the installation process.
double oil seal
Furthermore, authoritativeness in the field of double oil seals comes from well-documented research and successful implementation in complex mechanical frameworks. Companies that invest heavily in research and development are at the forefront of producing innovative double oil seal designs that push the boundaries of efficiency and reliability. Real-world evaluations and case studies conducted by these industry leaders highlight the measurable benefits of using high-quality double oil seals, reinforcing their indispensability in critical applications.
Trustworthiness, a cornerstone in the mechanical sector, is established through consistent performance and positive testimonials from long-term users. Trust in double oil seals is often built over years of reliable operation across diverse applications. Manufacturers of repute offer warranties and customer support that emphasize their commitment to quality and user satisfaction. These companies often provide comprehensive product information and technical support to assist users in choosing and applying the right double oil seal for their specific needs.
In conclusion, double oil seals are an indispensable component in maintaining machinery efficiency and reliability.
Their strategic application across various industries showcases their versatility and necessity. When chosen for the right application, installed correctly, and maintained with precision, double oil seals offer unmatched protection against wear and tear, ensuring that machinery operates at optimal levels. Stakeholders in engineering and mechanical fields must prioritize quality and expertise in the selection of double oil seals to safeguard their investments and achieve sustainable operational success.