Felt oil seals, an essential component in a myriad of mechanical systems, have been instrumental in maintaining the efficiency and longevity of machinery across various industries. Crafted from high-quality wool fibers, these seals serve as an effective barrier, preventing oil leakage and subsequent contamination of machinery components. Unlike their rubber or silicone counterparts, felt oil seals offer unique advantages in specific applications, proving their worth through decades of use.

The intrinsic properties of felt provide these seals with a distinct functionality. Felt's porosity is one of its key attributes, allowing it to absorb and retain lubricants while simultaneously resisting oil seepage. This capability not only enhances the lubrication of the moving parts but also reduces friction, thereby extending the life of machinery. The naturally compressible nature of felt enables it to conform to irregular surfaces, ensuring a snug fit and effective sealing even in challenging environments.
From a professional standpoint, the choice of felt oil seals can be advantageous in industries where noise reduction, vibration dampening, and temperature resilience are crucial. In the automotive sector, for example, felt oil seals are favored for their capacity to absorb sounds and reduce vibrations, contributing to a more silent and smoother operation of vehicles. Moreover, felt can withstand a range of temperatures, making it suitable for various applications, from heavy industrial machines to precision instruments.
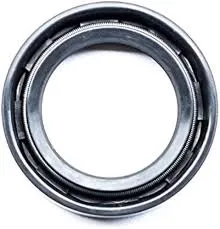
As an authoritative resource on sealing solutions, it is imperative to highlight the reliability of felt oil seals. Their performance in dusty, dirty, or abrasive conditions outshines many synthetic alternatives. Historically, felt oil seals have been a staple in agricultural machinery, demonstrating an impressive ability to endure harsh outdoor conditions. This reliability stems from their construction—felt's interlocking fibers offer a durable seal without the brittleness or cracking associated with some synthetic seals under thermal stress or UV exposure.
felt oil seal
The expertise in the manufacturing of felt oil seals involves understanding the blend of fibers and specific treatments to enhance their properties. It requires selecting the right wool grade, understanding the bonding process, and applying treatments to increase water and oil resistance. Manufacturers also conduct rigorous testing to ensure each seal meets the operational demands of its intended application. These steps ensure that felt oil seals not only meet but often exceed industry standards for longevity and performance.
Building trust with clientele involves providing clear insights into the maintenance and longevity of felt oil seals. For optimal performance, regular inspection and timely replacement are advised, especially in high-stress applications. It’s worth noting that, when appropriately cared for, felt oil seals can outlast many conventional options. Ensuring alignment, maintaining operational temperatures, and preventing excessive contamination can further augment their performance.
In conclusion, felt oil seals represent a vital blend of traditional craftsmanship and modern engineering prowess. Their ability to deliver reliability, especially in specialized or demanding environments, remains unmatched. By focusing on the unique properties of felt and its proven track record, professionals can confidently recommend these seals to clients seeking effective, economical solutions for their sealing needs. As a trusted advisor, staying informed about the latest advancements in felt oil seals and related technologies not only enhances your expertise but also positions you as a credible authority in the field.