The floating oil seal, also known as a face seal, is an indispensable component in various heavy machinery subjected to extreme working conditions. These seals are engineered to provide outstanding protection in harsh environments, ensuring the smooth and uninterrupted functioning of the equipment. Over the years, these seals have become a critical part of industries such as construction, mining, and agriculture, where reliability and longevity are paramount.

Understanding the intricacies of floating oil seals begins with their unique design. Unlike traditional seals that might degrade quickly under high pressure or abrasive conditions, floating oil seals consist of two identical metal rings and two corresponding rubber O-rings. The metal rings are lapped and polished to a mirror finish, minimizing friction and wear, which significantly extends the lifespan of the machinery.
The elastic rubber O-rings act as a buffer and keep the metal rings aligned. This innovative configuration allows the seals to 'float,' compensating for minor misalignments while maintaining an airtight closure.
In practical application, the effectiveness of floating oil seals is irrefutable. Consider earthmoving equipment like bulldozers or excavators, where seals must withstand constant exposure to dirt, mud, and water. A compromised seal could lead to detrimental downtime and costly repairs. The durability of a floating oil seal excels by rotating and moving with the axle, preventing foreign substances from entering critical components. Such reliability ensures machinery operates at optimal efficiency, decreasing maintenance expenses and extending service intervals.
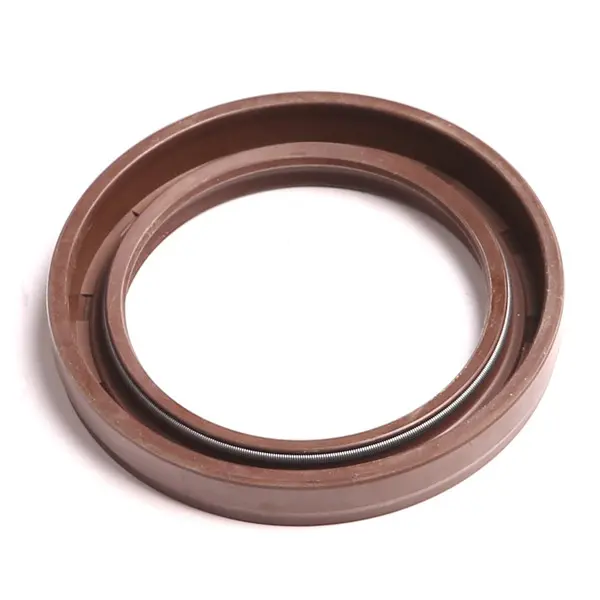
From an expert’s perspective, the installation of floating oil seals requires precision and a thorough understanding of the operating environment. It is crucial to select seals that are specifically designed for the equipment's application to maximize performance. For instance, seals meant for a high-temperature environment should be made from materials that can endure thermal expansion without losing structural integrity. Manufacturers often provide guidelines that detail the specifications and compatibility to aid engineers in making informed decisions.
floating oil seal
Industry veterans vouch for the authority and trustworthiness of floating oil seals, attesting to their high performance and reliability. These seals are rigorously tested to meet international standards, ensuring they deliver expected results in every conceivable condition. Such endorsement brings peace of mind to operators who rely on their machinery for day-to-day operations. Moreover, companies that produce these seals continuously innovate, using advanced technology to enhance the seals’ abilities, addressing new challenges as they arise.
Purchasing floating oil seals from reputable suppliers guarantees not only top-notch quality but also access to expert advice and support. Suppliers often extend comprehensive guides and consultation services, assisting clients in choosing the right seals and troubleshooting any issues that may occur during installation or operation. This level of service enhances trust between the supplier and customer, fostering long-term business relationships founded on shared success.
Overall, floating oil seals represent an indispensable element in machinery maintenance and optimization. Combining robustness with sophisticated engineering, they offer unmatched performance in the most demanding scenarios. For industries that depend heavily on equipment performance, investing in high-quality floating oil seals is a wise decision that promises substantial returns in operational efficiency and cost savings.