In the dynamic world of machinery and automotive industries, the framework oil seal stands as a pivotal component against the backdrop of complex mechanical systems. This device, seemingly modest in size, holds enormous significance in ensuring operational efficiency, longevity, and reliability of machinery. Delving into real-world applications, technical attributes, authoritative insights, and reliability factors, this article unravels the critical aspects that make the framework oil seal an indispensable ally in mechanical integrity.
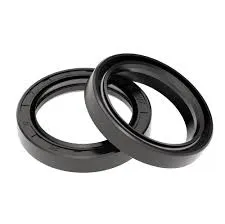
A framework oil seal is traditionally designed to protect and enclose various types of mechanical equipment. Its primary function is to seal and prevent leakages along the rotating shaft, effectively blocking contaminants and ensuring that the vital lubrication remains within. Essentially, this seemingly inconspicuous seal is an unsung hero in safeguarding the operational prowess of any machinery.
Engaging with industry experts reveals the framework oil seal's significance transcends mere sealing. It is engineered to accommodate thermal expansion, pressure variations, and angular misalignments—factors that commonly plague mechanical systems. Its resilience in harsh conditions, be it extreme temperatures or exposure to corrosive substances, showcases its superior material design, often composed of advanced elastomers and strong metallic reinforcement.
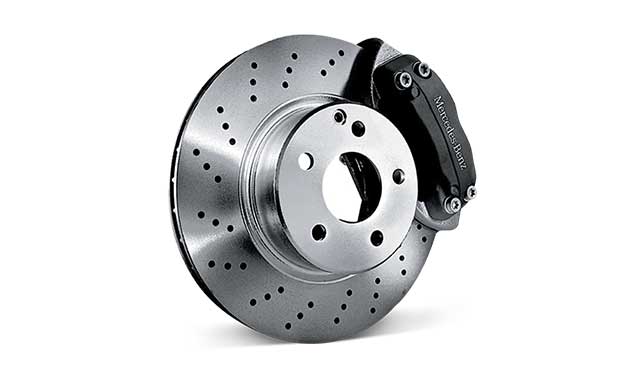
The science behind the framework oil seal is fascinating. Its functionality harnesses hydrodynamic principles to create a pressure profile along the seal's interface, preventing fluid leakage. Furthermore, precision manufacturing techniques have propelled modern oil seals into high-performance territories, offering lower friction, reduced wear, and enhanced durability.
From an expertise standpoint, the selection of a framework oil seal necessitates consideration of several parameters shaft speed, temperature extremes, pressure levels, and the type of fluid being contained. It is imperative to match these variables with the oil seal’s material properties to avert premature failures and ensure maximal efficiency. Specialists often recommend consulting with manufacturers for custom solutions, particularly for bespoke industrial applications where standard seals might not suffice.
framework oil seal
Authenticity and authority in framework oil seal manufacturing are often established through compliance with industry standards and certifications. Reputable manufacturers adhere to ISO standards,
a testament to their commitment to quality and safety. Moreover, possessing detailed product data sheets and offering after-sales support reinforces a company's credibility, providing end-users with necessary assurance about the seal’s performance and durability over time.
Trustworthiness is established not just by the product itself but by the ecosystem surrounding it. Technicians, engineers, and maintenance personnel all play integral roles in the life cycle of a framework oil seal. Their feedback can be invaluable in refining design and performance scopes. Equally important is the end-user's role in maintaining the oil seal's functionality through regular inspection and timely replacement upon showing signs of wear and tear.
Environmentally, the role of the framework oil seal is often underestimated. By preventing oil and fluid leakages, these seals contribute to reducing environmental hazards and promote sustainability in industrial practices. The conscientious design and utilization of framework oil seals can, therefore, directly influence a company’s environmental footprint—a growing concern amid tightening regulatory landscapes.
Technological advancements hint at a promising trajectory for the future of framework oil seals. With the adoption of smart sensors, real-time monitoring and predictive maintenance of seals could soon become the norm, drastically curtailing downtime and elevating mechanical reliability. As industries increasingly transition to more automated processes, the integration of IoT and AI technologies in oil seal monitoring presents a new dimension for operational efficiencies.
In summary, the framework oil seal may be a secondary player to laypersons within mechanical narratives, yet it is undeniably a cornerstone in operational integrity and efficiency. Its continued evolution, spurred by technological and material innovations, holds significant implications for industries reliant on mechanical operations. Therefore, understanding and leveraging its capabilities is a substantive step toward achieving and maintaining peak mechanical performance.