Choosing the right gasket for industrial applications is crucial for ensuring optimal performance, safety, and longevity of equipment. Among the many options available, the full face rubber gasket stands out due to its versatility and robust sealing capabilities. This article delves into the expert insights, real-world experiences, and industry best practices surrounding the use of full face rubber gaskets, emphasizing their importance and trustworthiness in demanding environments.
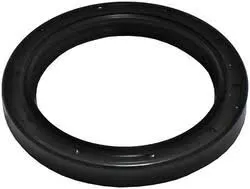
Full face rubber gaskets are designed to cover the entire flange face, providing a broad sealing area that enhances the efficiency and reliability of piping systems. This design minimizes the risk of leaks in high-pressure and high-temperature applications, which is particularly advantageous in critical industries such as petroleum, chemical processing, and pharmaceuticals.
Experts in the field of fluid dynamics and industrial engineering often recommend full face rubber gaskets for applications where a secure and resilient seal is paramount. The material properties of rubber, including its flexibility, resilience, and chemical resistance, make it an excellent choice for creating gaskets that can withstand a wide range of operational conditions. The inherent flexibility of rubber allows the gasket to conform to surface irregularities, ensuring a tight seal even on less-than-perfect flange surfaces.
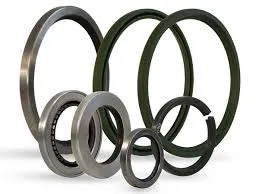
The expertise behind the design and manufacturing of full face rubber gaskets is rooted in extensive research and development. Industry leaders invest heavily in understanding the behavior of rubber materials under various environmental conditions to enhance the performance characteristics of these gaskets. This dedication to innovation has resulted in gaskets that not only meet but often exceed industry standards for safety and durability.
full face rubber gasket
Real-world applications further demonstrate the reliability of full face rubber gaskets. For instance, in the chemical industry, these gaskets play a vital role in preventing the escape of hazardous substances. By providing a dependable sealing solution, they protect both the workforce and the environment from potential harm. Companies that utilize full face rubber gaskets can attest to their long-term cost efficiency; minimizing downtime and maintenance costs often results in substantial financial savings.
Beyond the technical specifications, the authority of full face rubber gaskets in the industry is established through compliance with stringent quality standards and regulations. Reputable manufacturers rigorously test their products, ensuring they comply with ISO standards and other relevant certifications. This level of scrutiny is essential for building trust among users, as it assures them of the product’s capability to perform under the most challenging conditions.
Choosing a full face rubber gasket from a trusted manufacturer also ensures a level of credibility that is indispensable in mission-critical applications. The use of inferior or uncertified components can lead to catastrophic failures, underscoring the importance of opting for reputable suppliers who prioritize quality and safety.
In conclusion, full face rubber gaskets fulfill an essential role in industrial applications requiring robust sealing solutions. Their combination of material strengths, expert engineering, and proven field performance solidifies their status as a reliable component in various sectors. When selected and implemented properly, these gaskets can significantly enhance the efficiency, safety, and operational longevity of industrial systems. Industry professionals recognize and trust full face rubber gaskets as an indispensable part of their toolkit for maintaining high standards of performance and safety across the board.