Choosing the right gearbox oil seal is essential for maintaining the longevity and efficiency of industrial machinery. An oil seal plays a crucial role in lubricating gears, preventing leakages, and protecting the system from contaminants. The optimal selection and maintenance of these seals demand a comprehensive understanding of their functionality, material composition, and application environments.
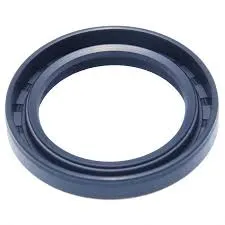
An oil seal's primary function is to protect the gearbox from leaking lubricants and external contamination. It is typically a circular component that fits snugly between the moving parts of machinery, maintaining the balance of oil pressure and preventing spillages. Given the intricate nature of gear systems, the integrity of these seals directly influences operational efficacy, reducing downtime and lowering maintenance costs.
Expertise in oil seal selection involves understanding the variety of materials used in their manufacture—nitrile rubber, fluoroelastomer, and silicone, to name a few. Each material offers distinct advantages. Nitrile rubber, for instance, is cost-effective and resistant to petroleum oils, making it suitable for general applications. In contrast, fluoroelastomers are prized for their resilience to high temperatures and aggressive chemicals, ideal for demanding industrial settings. Selecting the appropriate material enhances the seal's performance and extends its service life.
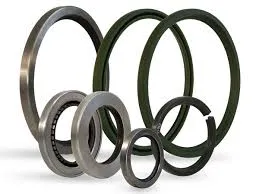
Installing an oil seal requires precision. A misaligned or improperly installed seal can lead to early wear, leaks, and potential machinery failure. Therefore, proper tools and techniques—like using a seal driver and ensuring a clean environment—are fundamental to a successful installation. It's crucial to follow manufacturer guidelines while installing these components to maintain their effectiveness.
gearbox oil seal
In the realm of expertise, engineers emphasize the importance of regular inspection and maintenance of gearbox oil seals to ensure they remain in optimal condition. Over time, seals can degrade due to exposure to harsh conditions, leading to small tears or warping. Regular checks for signs of wear and tear, such as oil leaks or unusual noises, are vital. When defects are detected early, seals can be replaced before more significant damage occurs, thus ensuring continuing operational efficiency.
Within industrial contexts, where heavy-duty equipment operates, the robustness of an oil seal is essential. Gearbox oil seals must withstand extreme pressures and temperatures, maintaining their structural integrity. Utilizing seals that meet industry standards from reputable manufacturers, backed by certifications like ISO or OEM, contributes significantly to the credibility and reliability of these components.
Trustworthiness in the products selected is enhanced by choosing suppliers with a longstanding track record in the industry. Reading reviews, asking for performance data, and verifying the pedigree of a brand can help ensure that the oil seals purchased will meet the demands of industrial applications. A trustworthy product reduces the risk of failures and associated costs, offering peace of mind to machinery operators.
To sum up, understanding the intricacies involved in selecting and maintaining gearbox oil seals is paramount for optimal operation. By choosing the right materials, ensuring correct installation, and maintaining a strict regime of inspections, businesses can enhance the durability and performance of their machinery. Such a proactive approach not only ensures the smooth operation of industrial gearboxes but also extends their lifespan, providing a solid return on investment. Empowering your operations with the most suitable gearbox oil seals signals not only expertise but a commitment to excellence and reliability.