The Ubiquitous Role of Thin Rubber Gaskets in Modern Industry
A thin rubber gasket, seemingly insignificant in size and appearance, plays an essential role in a myriad of industries, from automotive to aerospace, plumbing to electronics. This compact, yet resilient component is the silent guardian of seals, ensuring leak-proof connections and maintaining operational efficiency.
A gasket, by definition, is a thin, usually circular, rubber or elastomeric material used to fill the space between two mating surfaces, preventing leakage from or into the joined parts. The term 'thin rubber gasket' refers specifically to those with minimal thickness, often less than a millimeter, yet their impact is disproportionately large.
The versatility of thin rubber gaskets lies in their adaptability. They can be customized to fit various shapes and sizes, making them suitable for diverse applications. Their rubber composition, whether it's natural rubber, silicone, neoprene, EPDM, or Viton, imparts unique properties such as resistance to heat, cold, chemicals, and pressure, making them ideal for harsh environments.
In the automotive industry, thin rubber gaskets ensure the integrity of engine compartments by sealing oil pans, cylinder heads, and fuel lines. In plumbing, they prevent water leaks in pipe connections. In electronics, their insulating properties protect sensitive components from electrical currents and moisture. Aerospace engineering also relies on these gaskets for sealing aircraft cabins, fuel tanks, and hydraulic systems.
The manufacturing process of thin rubber gaskets involves precision cutting or molding techniques. The raw rubber material is first compounded with specific additives to enhance its properties, then shaped into the desired form The raw rubber material is first compounded with specific additives to enhance its properties, then shaped into the desired form
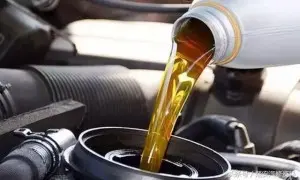
The raw rubber material is first compounded with specific additives to enhance its properties, then shaped into the desired form The raw rubber material is first compounded with specific additives to enhance its properties, then shaped into the desired form
thin rubber gasket. Post-production, quality control checks are rigorous to ensure each gasket meets stringent standards for durability and performance.
Despite their thinness, these gaskets exhibit exceptional durability. They can withstand repeated compression and decompression without losing their sealing ability, a testament to their inherent resilience. However, like all materials, rubber gaskets do degrade over time, necessitating regular inspection and replacement.
The importance of a thin rubber gasket cannot be overstated. It is a small but critical element that safeguards equipment functionality, prevents costly leaks, and maintains overall system integrity. As technology advances and industries evolve, the demand for more specialized and efficient gaskets will only increase. Thus, the study and development of thin rubber gaskets remain a vital area of research and innovation in the world of engineering and manufacturing.
In conclusion, the thin rubber gasket, a humble component in our daily lives, silently performs a crucial function. Its significance extends far beyond its size, serving as a protective barrier in countless applications. Its durability, versatility, and customizability make it a staple in modern industrial practices, and its continued evolution will undoubtedly play a key role in shaping future technologies.