High pressure rubber gaskets are crucial components in industries that require a reliable seal under high pressure conditions. These gaskets are designed to withstand extreme conditions, including high temperatures, intense pressures, and various chemical exposures. As an experienced industry expert, understanding the intricacies of high pressure rubber gaskets is fundamental to ensuring the optimal performance and longevity of your systems.
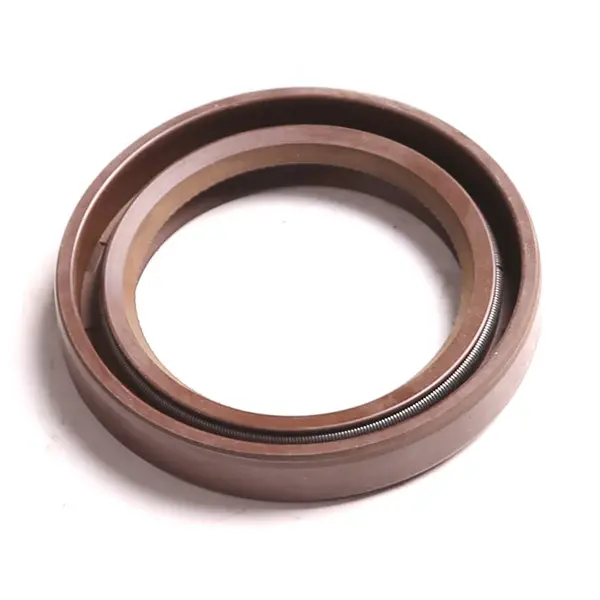
The primary function of a high pressure rubber gasket is to fill the space between two or more mating surfaces, preventing leaks while under compression. The gasket must maintain a robust seal, designed to cope with fluctuating temperatures and pressures that could potentially compromise the integrity of less durable materials. Rubber gaskets offer the flexibility and resilience necessary to adapt to these challenges, ensuring they maintain their sealing properties over prolonged periods of use.
Selecting the appropriate material is a cornerstone of gasket performance. Synthetic rubbers such as EPDM, nitrile, and neoprene are frequently used for high pressure applications due to their excellent resistance to oils, chemicals, and deterioration under severe environmental conditions. EPDM, for example, boasts superior resistance to heat and steam, making it ideal for dynamic environments where thermal cycling could otherwise lead to seal failures.
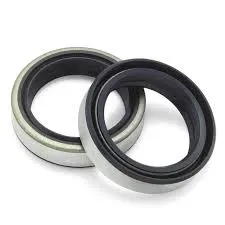
In industries such as oil and gas, chemical processing, and industrial machinery, the demand for high pressure rubber gaskets is synonymous with the need for safety and reliability. Failures in these systems often lead to catastrophic outcomes, underscoring the importance of using high-quality gaskets that have been subjected to rigorous testing and quality assurance processes. Standards such as those set by the American Society for Testing and Materials (ASTM) provide guidelines for these gaskets, ensuring they meet the required specifications to safely perform under designated conditions.
One of the key elements impacting gasket performance is proper installation. Even the highest quality gaskets can fail if not installed correctly. It's crucial to ensure that the gasket is appropriately sized and aligned, and that the mating surfaces are clean and free from debris. Additionally, the proper torque must be applied to the flange bolts to secure the gasket without causing excess compression, which can lead to premature failure.
high pressure rubber gasket
Recent advancements in material science have led to the development of hybrid gaskets that combine the elasticity of rubber with the strength of composite materials. These innovations offer enhanced performance, providing a more effective seal and extending the service life of the gasket in ultra-high pressure settings. Companies continually investing in research and development are likely to stay ahead of the curve, adapting quickly to the evolving demands and challenges faced by modern industry applications.
From a practical standpoint, consistent maintenance and inspection routines are paramount. Regular assessments of gasket conditions help identify wear and tear or potential for leaks before they escalate into more severe issues. Thermographic imaging and ultrasonic leak detection devices are modern methods used to examine the integrity of seals without needing to dismantle equipment completely.
Trust is cultivated through a commitment to quality and safety, positioning suppliers and manufacturers of high pressure rubber gaskets as authoritative voices in their field. When sourcing these essential components, turning to certified and reputable suppliers should be a priority, ensuring that every gasket employed within your operations upholds the highest standards of performance and reliability.
Navigating the complexities of high pressure environments demands not only high-caliber products but also a deep understanding of their application, supporting industries in maintaining operational success and safety.