Hydraulic oil seals play a critical role in industrial machinery, acting as the barrier that prevents leakage of lubricants or hydraulic fluids. These components, though small, uphold the integrity of entire hydraulic systems, ensuring smooth operations across various applications. Understanding the design, functionality, and material composition of hydraulic oil seals is crucial for maintaining system reliability and performance.
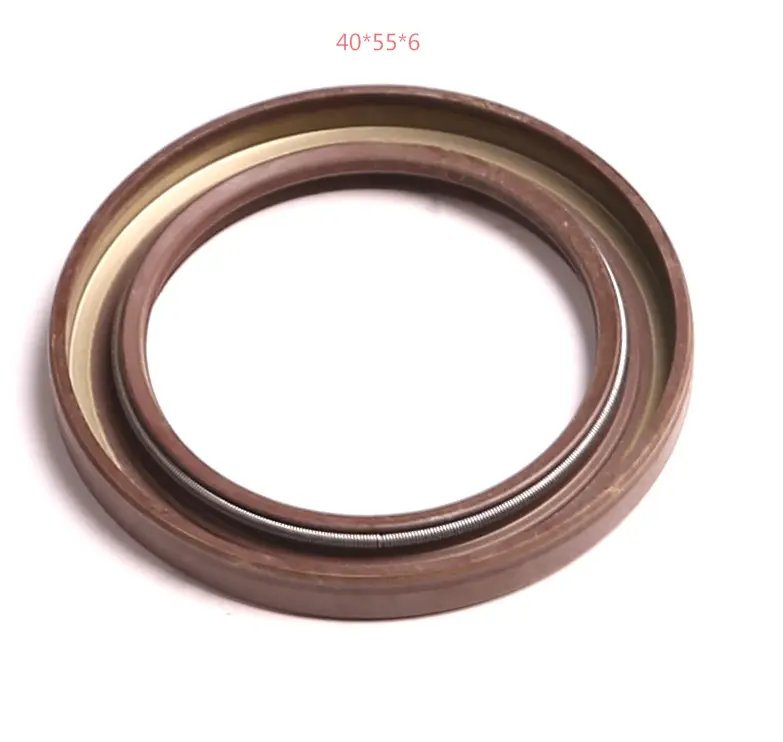
Manufacturers design hydraulic oil seals with precision, employing materials like nitrile rubber, fluorocarbon, or silicone, each offering unique advantages. Nitrile rubber, for instance, is chosen for its excellent resistance to oils and its affordability, making it ideal for standard environments. On the other hand, fluorocarbon provides superior resistance to high temperatures and chemicals, thus fitting perfectly in extreme conditions where standard materials might fail.
Installation procedures deserve meticulous attention. Improper installation can lead to premature seal failure, resulting in costly downtime. It requires understanding the exact dimensions and specifications for the sealing environment. Ensuring that the shaft and housing are free from damage and debris is paramount, as surface imperfections can lead to leaks. Proper lubrication during installation, following manufacturer recommendations, can enhance the seal life significantly.

Regular maintenance and inspection of hydraulic oil seals prevent unexpected failures. Inspect the seals periodically for signs of wear or damage, such as hardening, cracking, or dimensional changes. Implementing a proactive maintenance schedule based on the operating conditions and manufacturer guidelines prolongs the operational lifespan of both the seals and the equipment they protect.
hydraulic oil seals
The authority of experienced maintenance technicians and engineers heavily influences the best practices for handling hydraulic oil seals. Their expertise facilitates the selection of appropriate seals for specific applications, taking into account factors like pressure, temperature, and environmental conditions. Such expertise ensures that not only performance standards are met, but also enhances the overall efficiency of the hydraulic system.
In terms of sustainability, the choice of hydraulic seals can impact the environmental footprint of a machinery operation. Opting for seals manufactured with environmentally friendly materials or those designed to extend service life can contribute to sustainability goals. Some manufacturers are now developing seals with recyclable materials without compromising performance, a testament to innovation in response to modern ecological challenges.
The credibility of hydraulic oil seals is backed by extensive testing and certifications. Suppliers often provide detailed data sheets outlining a seal's properties, performance in various conditions, and compatibility with different hydraulic fluids. These documents serve as a reliable resource for engineers and procurement specialists, ensuring that every seal meets stringent quality standards.
Ultimately, hydraulic oil seals are indispensable components, safeguarding the efficiency and longevity of hydraulic systems. Their design, material selection, and maintenance are areas that require thorough understanding and expertise. By prioritizing these aspects, industries not only enhance operational reliability but also support sustainable practices, aligning with the broader move towards greener technologies. Whether for a novice technician or a seasoned engineer, knowing the nuances of hydraulic oil seals is pivotal for success in today's competitive industrial landscape.