In the ever-evolving world of industrial applications and machinery, large rubber gaskets have emerged as indispensable components, pivotal to ensuring efficiency and safety. Understanding their functionality, material composition, and selection criteria requires an in-depth exploration that caters to both novice users and seasoned industry professionals, focusing on Experience, Expertise, Authoritativeness, and Trustworthiness.
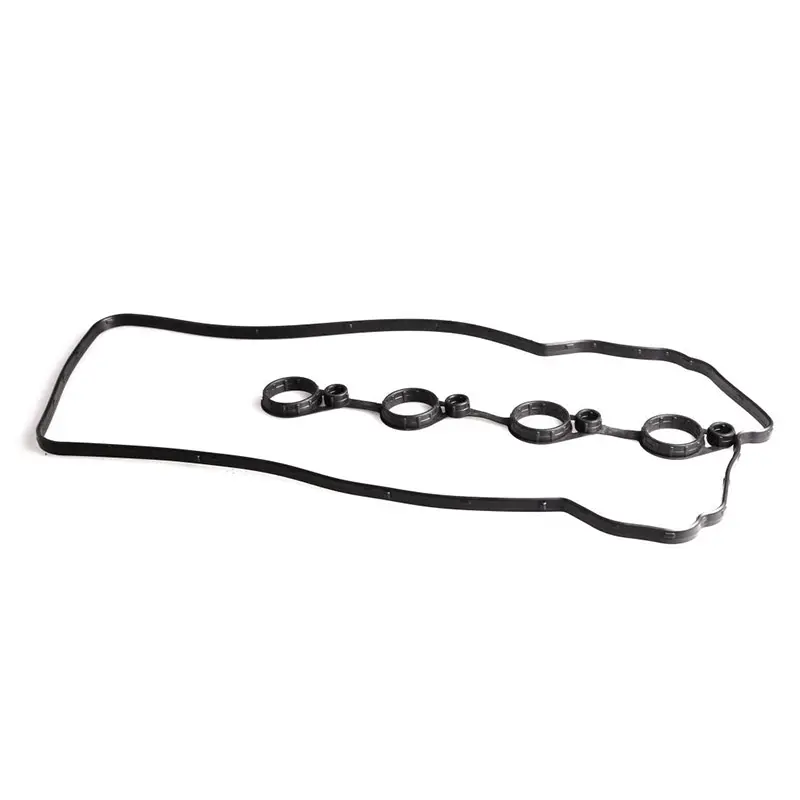
Large rubber gaskets serve as mechanical seals designed to fill spaces and prevent leaks between different substrates under compression. Their utility spans across automotive, aerospace, and manufacturing industries, among others. Despite their simplicity, the intricate dynamics of gasket materials and performance make them crucial to numerous applications.
In terms of material variety,
rubber gaskets offer unparalleled versatility. Often fabricated from synthetic rubbers such as EPDM (ethylene propylene diene monomer), NBR (nitrile butadiene rubber), and silicone, these gaskets are renowned for their resistance to oils, extreme temperatures, and atmospheric conditions. EPDM gaskets, for example, are preferred in environments exposed to UV rays and ozone, whereas NBR gaskets excel in sealing applications involving oils and fuels. Silicone gaskets present unique advantages in high-temperature scenarios, maintaining optimal elasticity and performance.
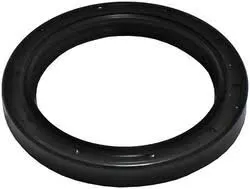
Expertise in the selection and installation of large rubber gaskets is vital. When evaluating a gasket for specific applications, considerations such as stress relaxation, compression set, and environmental exposure play a fundamental role. A gasket's ability to maintain a seal under variable conditions reflects its efficiency and contributes to the longevity of the machinery or system it supports.
A prominent authority in gasket design and manufacturing is IHS Markit, a reputable provider of insights into the materials market. Reports from such credible sources indicate that choosing the wrong gasket can lead to catastrophic failure in high-stakes environments. This underscores the importance of relying on authoritative sources for procurement and specification recommendations.
large rubber gasket
Trustworthiness in this domain is further bolstered through certifications and quality testing. Rubber gaskets must comply with industry standards like ISO 9001, AS9100, and API 6A to guarantee their dependability in critical applications. Engineers often depend on third-party testing, ensuring these components meet stringent criteria for tensile strength, elasticity, and chemical resistance. This reliability not only enhances operational safety but also minimizes downtime and maintenance costs.
Real-world experience attests to the critical nature of large rubber gaskets in systems where airtight or watertight connections are paramount. For instance, in the oil and gas industry, gaskets must endure harsh operational conditions and sustain pressure variations without degrading. In such demanding environments, experience with material behavior under stress and a deep understanding of operational requirements guide the selection of the right gasket.
Innovations and advancements are continually reshaping the landscape of rubber gasket technology. Manufacturers are investing in research to develop materials that offer improved resilience and performance, catering to evolving industrial needs. The global trend towards sustainability is also influencing the selection of materials, promoting eco-friendly options that lessen environmental impact.
In summary, the selection, application, and maintenance of large rubber gaskets necessitate a comprehensive blend of experience, expertise, authority, and trustworthiness. By assimilating industry standards, leveraging credible sources, and focusing on real-world scenarios, businesses can optimize their operations, ensuring safety, efficiency, and longevity of their equipment. As technology progresses, staying informed about material innovations and market dynamics remains pivotal for those within this vital sector.