In industrial settings where precision sealing is crucial, locking gaskets emerge as a failsafe component that enhances durability and effectiveness. These accessories, often overlooked, play a pivotal role, preventing leaks and ensuring that mechanical systems function efficiently. Unlike typical gaskets that merely compress between surfaces, locking gaskets offer a unique grip, retaining their place even under stress, vibration, or thermal expansion. This characteristic renders them indispensable in industries such as aerospace, automotive, and manufacturing, where the stakes are high, and equipment integrity is paramount.
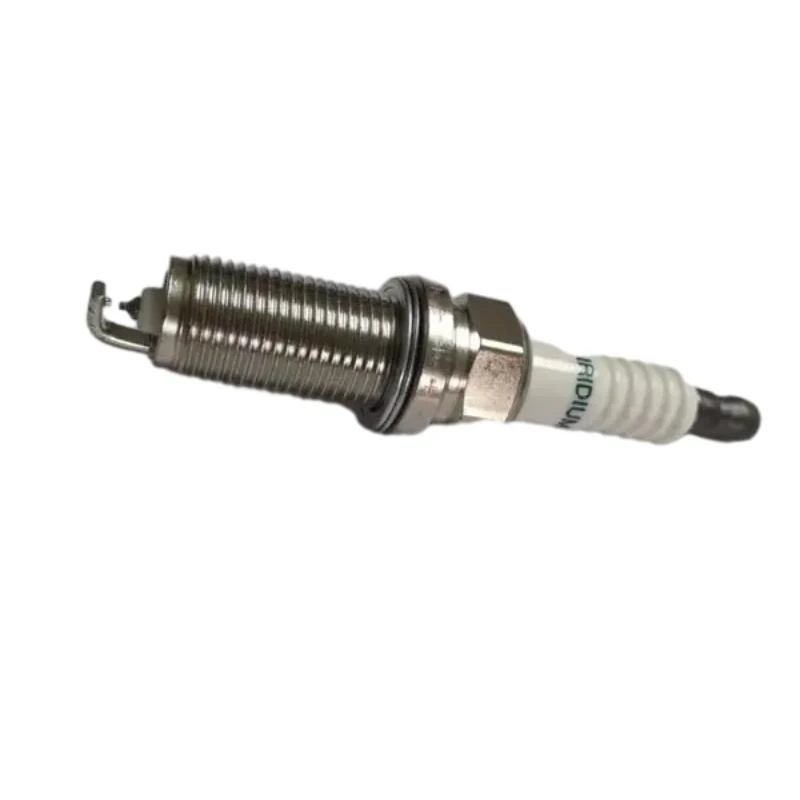
Professionals in these fields leverage locking gaskets for their ability to form a more reliable seal compared to traditional options. Their design often includes an interlocking feature, which acts like a secure handgrip between the sealing surfaces, reducing the risk of dislodgement. These mechanical advantages are coupled with material innovations; for instance, neoprene and EPDM are frequently used due to their resilience against chemical exposure and extreme temperatures. This combination of design and material ensures that locking gaskets maintain their function under diverse operational conditions.
From an engineering perspective, implementing the correct type of locking gasket can significantly streamline maintenance efforts. Their robustness mitigates the frequency of replacement, thus saving time and reducing costs associated with downtime. In scenarios where maintenance is inevitable, the locking feature facilitates easier removal and reinstallation, a testament to their intelligent design.
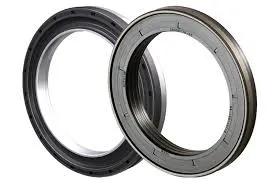
Beyond mechanical advantages, locking gaskets also contribute to safety improvements. In environments susceptible to leaks of gases or liquids, the failure of a seal can lead to catastrophic outcomes.
Locking gaskets provide that additional layer of protection, minimizing risks and enhancing overall safety protocols. This reliability fosters trust among engineers and safety inspectors, who recognize and value components that contribute to operational safety.
locking gasket
Authoritative voices in the industry, such as engineers and product developers, advocate for the use of locking gaskets due to their transformative impact on product life cycles. Journals in the mechanical and aerospace domains frequently publish case studies underscoring the cost-effectiveness and performance benefits of these gaskets. The recurring theme is clear incorporation of locking gaskets is not merely a trend, but a step forward in the evolution of industrial design thinking.
For companies committed to sustainability, locking gaskets also offer an edge. By extending the longevity of mechanical seals, they contribute to a reduced frequency of part replacement, which, in turn, decreases material waste. This aspect, coupled with the ability to recycle certain types of gaskets, aligns with broader environmental goals, appealing to businesses striving for greener operations.
Purchasing and installing locking gaskets necessitates understanding specific needs and constraints of the machinery involved. Enterprises must consider environmental conditions, chemical exposures, and mechanical pressures to choose the most appropriate type of gasket. Consulting with suppliers and engineers helps in making informed decisions that balance performance needs with budget constraints.
In summation, locking gaskets exemplify a fusion of simplicity and innovation, offering elevated performance in sealing applications across various industries. Their ability to deliver long-lasting seals, reduce maintenances costs, and enhance safety standards make them a compelling choice for industry leaders aiming to boost efficiency and reliability. For anyone engaged in fields where machinery and reliability intersect, understanding and leveraging the advantages of locking gaskets is not only beneficial but essential to staying competitive in a technology-driven marketplace.