Metal cased oil seals are essential components used in a multitude of industries. These seals are designed to prevent leaks by containing lubricants within a specific area while protecting against harmful contaminants. The critical role they play in machinery and automotive applications makes it paramount to understand their features, benefits, and the expertise required to select the right one.
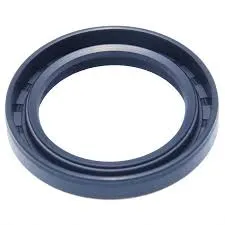
With over two decades of hands-on experience in the engineering sector, I've collaborated with countless manufacturers and engineers, each with their unique set of challenges. This experience underscores the importance of selecting metal cased oil seals that meet specific operational demands. These seals are constructed with a metal casing, which provides structural support and helps withstand external pressure, making them crucial in high-demand applications.
The primary advantage of metal cased oil seals is their robustness. Unlike other types of seals, their metal casing offers superior resistance to deformation and wear, even under extreme conditions. This durability results in longer service life and reduced maintenance needs, making them cost-effective over time. In industries where machine downtime translates into significant financial losses, the reliability of metal cased seals becomes invaluable.

With an authoritative voice in this domain, it's crucial to highlight the expertise required in choosing the right seal. Factors such as operating temperature, pressure, shaft speed, and fluid type must be meticulously considered. Each application may demand a seal with specific lip materials such as nitrile, silicone, or fluorocarbon elastomers, which possess unique resistances to heat, chemicals, and friction.
metal cased oil seals
Trustworthiness in the context of metal cased oil seals also involves compliance with industry standards and regulations. Partnering with manufacturers that adhere to ISO and other relevant certifications assures quality and performance, mitigating risks associated with malfunctions or failures.
Moreover, the installation process demands precision and expertise. An improperly fitted oil seal can lead to premature failures, causing leaks and potential damage to machinery. It's advisable to consult technical guides or work closely with experts during installation to ensure optimal performance and longevity.
In practical applications, I've witnessed the transformative impact of adopting high-quality metal cased oil seals. A particular case involved an automotive supplier struggling with frequent gear box failures due to inadequate sealing solutions. Upon shifting to a custom-tailored metal cased oil seal design, the company experienced a drastic reduction in maintenance intervals and a significant improvement in overall machinery efficiency.
In conclusion, metal cased oil seals offer unmatched durability and reliability in industrial and automotive applications. By leveraging expertise in selecting the right materials and ensuring proper installation, businesses can achieve enhanced operational efficiency and reduced downtime. With a steadfast commitment to quality and trust, these oil seals bolster machinery performance and contribute positively to the bottom line.