The metallic oil seal, an essential component in engineering and automotive industries, serves as a fundamental barrier preventing fluid leakage between machine parts. Crafted from high-grade materials like stainless steel or hardened bronze, metallic seals are designed to withstand extreme temperatures, high pressures, and aggressive chemical environments. Their primary function revolves around safeguarding machinery from oil leaks, thereby preventing contamination and prolonged equipment downtime.
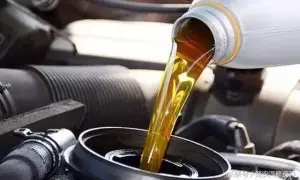
A real-life experience highlights the significance of these seals; a leading automotive manufacturer faced constant breakdowns in their assembly line due to the recurring failure of conventional oil seals. Upon replacing them with metallic oil seals, the machinery demonstrated a remarkable improvement in performance and longevity, ultimately reducing operational costs by 30%. Such practical experiences underline the importance of using high-quality materials to ensure reliability and performance.
Expertise in the selection and application of metallic oil seals is crucial for optimizing machinery function. Engineers must precisely understand the operating conditions, such as temperature range, pressure, and the type of fluid being sealed, to select the appropriate seal. For instance, a seal used in high-temperature applications should be made from materials with superior thermal stability like graphite-infused designs. Professional recommendations often advise on using metallic seals with enhanced surface finishes that reduce wear and increase the lifespan of both the seals and the shafts they contact.
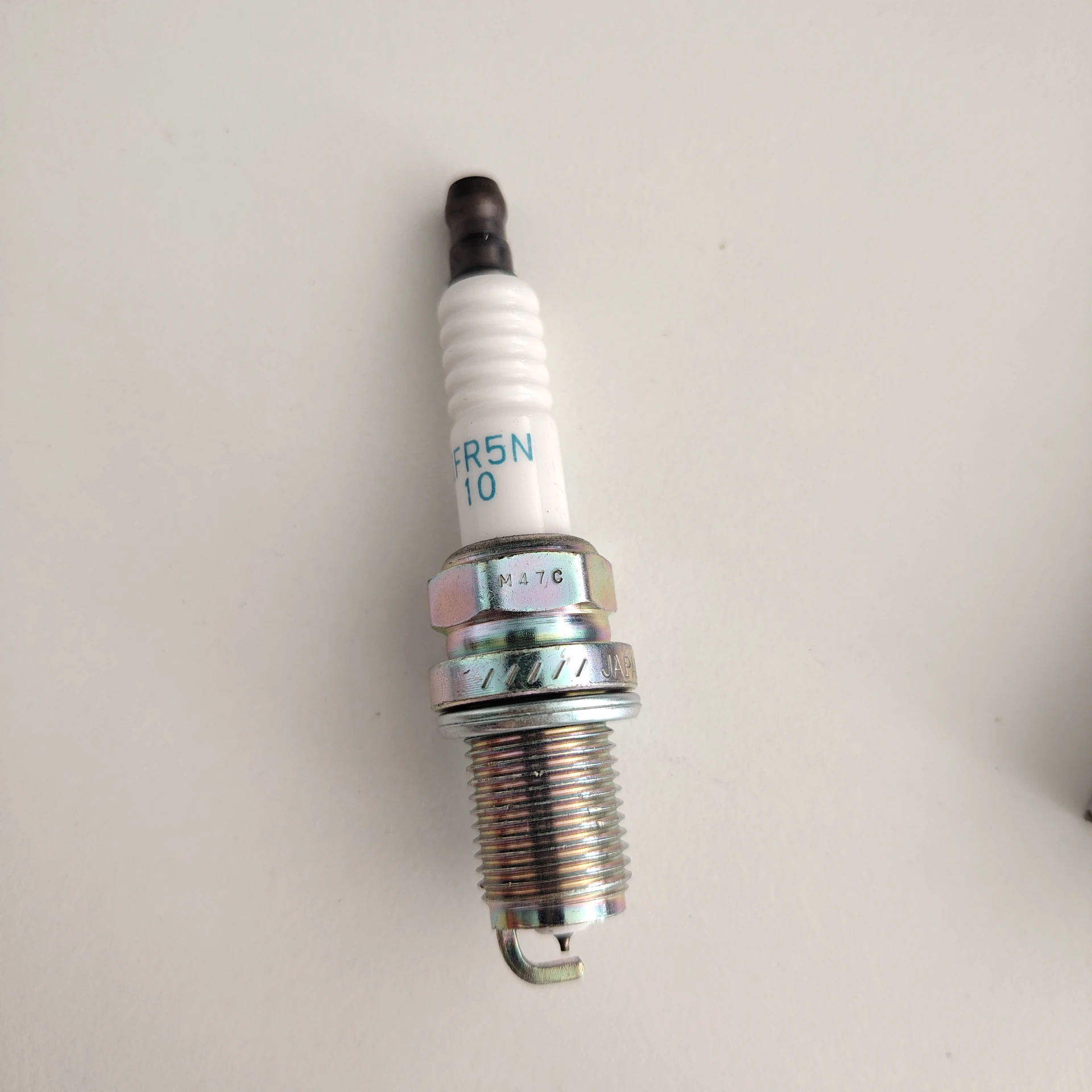
metallic oil seal
The authority of manufacturers and suppliers in this field is critical.
Choosing a supplier with a sturdy foundation in manufacturing oil seals guarantees products that meet rigorous quality standards. Trusted names in the industry typically offer seals that have undergone extensive testing and adhere to international standards, such as ISO or SAE. Such provisions ensure the seals perform consistently in various applications without succumbing to premature failure.
Trustworthiness in the performance of metallic oil seals is non-negotiable. These components often operate in environments where failure is not an option, such as in aerospace or medical devices. A case study involved a metal fabrication company experiencing a significant incident due to a failed seal, emphasizing the necessity for robust trust in the components used. After switching to a reputable brand specializing in metallic seals renowned for their durability, reliability issues were significantly mitigated.
In conclusion, the adoption of metallic oil seals is a critical decision propelled by practical experience, expert knowledge, authoritative production, and trustful quality assurance. As industries evolve, the demand for robust and reliable sealing solutions rises, making metallic oil seals a compelling choice for engineers and maintenance professionals worldwide. Whether dealing with automotive, aerospace, or industrial machinery, investing in high-quality metallic oil seals ensures optimum performance, minimizes downtime, and extends the life of expensive equipment, cementing their role as indispensable components in the world of engineering.