Oil Seal A Crucial Component in Machinery Performance
Oil seals are integral components in the operation of machinery, serving as a barrier between the lubricating oil and the external environment. Their primary function is to prevent the leakage of oil from the system while allowing the rotation of the shaft. The performance of these seals is critical to the overall efficiency and longevity of the machinery.
One of the key factors that determine the effectiveness of an oil seal is its material composition. Common materials used in oil seals include rubber, fluoropolymer, and synthetic materials like PTFE (polytetrafluoroethylene). Each material offers unique properties that make it suitable for specific applications. For instance, rubber seals are known for their flexibility and resistance to oil and heat, making them ideal for low-pressure environments. On the other hand, PTFE seals are highly durable and resistant to extreme temperatures and chemicals, making them suitable for high-pressure and harsh conditions.
The design of an oil seal also plays a significant role in its performance. Factors such as the shape of the seal, the type of lip material, and the presence of additional features like springs or backup rings can all affect how well the seal performs Factors such as the shape of the seal, the type of lip material, and the presence of additional features like springs or backup rings can all affect how well the seal performs
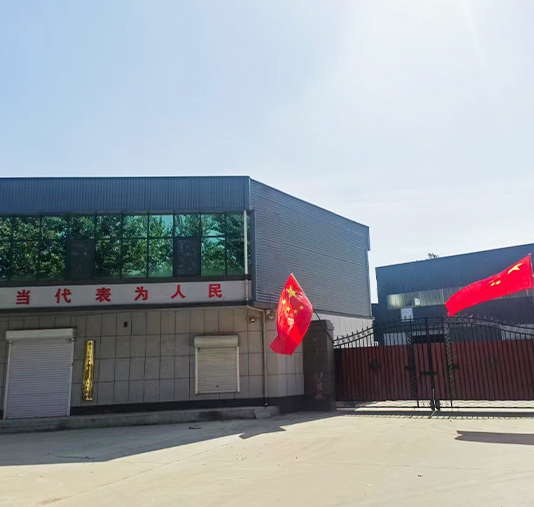
Factors such as the shape of the seal, the type of lip material, and the presence of additional features like springs or backup rings can all affect how well the seal performs Factors such as the shape of the seal, the type of lip material, and the presence of additional features like springs or backup rings can all affect how well the seal performs
oil seal 25 40 7. For example, a lip seal with a V shape can create a tighter seal by exerting more pressure on the shaft, while a backup ring can provide additional support and prevent extrusion under high pressures.
The correct installation of an oil seal is also crucial for its long-term performance. Improper installation can lead to damage to the seal, reducing its effectiveness and potentially causing leaks. It is essential to follow the manufacturer's instructions carefully when installing an oil seal to ensure that it is properly seated and aligned.
In conclusion, oil seals are indispensable components in the operation of machinery. Their performance is influenced by factors such as material composition, design, and installation. By selecting the right material and design for their specific application, and ensuring proper installation, engineers can help ensure the long-term reliability and efficiency of their machinery.