Oil Seal The Crucial Component in Machinery Performance
In the realm of machinery and equipment, the oil seal serves as a vital component, ensuring smooth operation and extending the life of the machine. This tiny yet indispensable part is designed to prevent the leakage of oil or other fluids from the system while allowing the rotation of shafts or pistons without any hindrance.
The functionality of an oil seal is predicated on its ability to create a tight seal between two moving parts, such as a shaft and a housing. It achieves this by utilizing a combination of materials, designs, and sealing elements that adapt to various operating conditions. These include rubber,PTFE, and other synthetic materials that provide excellent resistance to heat, chemicals, and wear.
One of the primary functions of an oil seal is to prevent the leakage of oil from the engine, transmission, or hydraulic system. This is crucial because oil is the lifeblood of these systems, providing lubrication, cooling, and cleaning agents that are essential for optimal performance. A leak can lead to reduced efficiency, increased wear, and even catastrophic failure if not addressed promptly.
Moreover, oil seals also prevent contaminants from entering the system. Dirt, dust, and other debris can cause significant damage to the moving parts if they are allowed to enter the system. By acting as a barrier, oil seals help maintain the cleanliness of the system and ensure that it operates smoothly By acting as a barrier, oil seals help maintain the cleanliness of the system and ensure that it operates smoothly
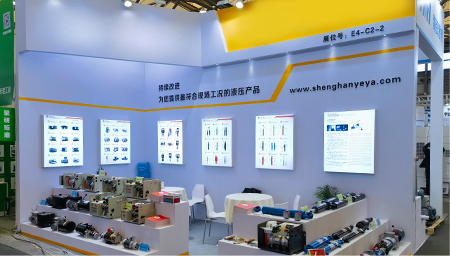
By acting as a barrier, oil seals help maintain the cleanliness of the system and ensure that it operates smoothly By acting as a barrier, oil seals help maintain the cleanliness of the system and ensure that it operates smoothly
25x41 25x6 oil seal.
In addition to their functional benefits, oil seals also contribute to the overall safety and reliability of machinery. By preventing leaks and contamination, they help reduce the risk of accidents and downtime, which can be costly for businesses. Furthermore, high-quality oil seals can withstand extreme temperatures, pressures, and speeds, making them suitable for use in a wide range of applications.
When selecting an oil seal, it is important to consider factors such as the type of fluid being sealed, the temperature and pressure ranges, and the speed at which the shaft or piston will rotate. This will help ensure that the seal is compatible with the specific requirements of the application and will provide the necessary level of protection.
In conclusion, oil seals play a critical role in maintaining the performance and longevity of machinery and equipment. By preventing leaks and contamination, they help ensure smooth operation and reduce the risk of accidents and downtime. With their diverse range of materials and designs, oil seals can be tailored to meet the unique requirements of any application. As such, it is essential to choose the right oil seal for the job to ensure optimal performance and long-term reliability.