Industrial Oil Seals Crucial Components in Machinery Performance
In the realm of industrial machinery, oil seals play a pivotal role. These critical components are designed to prevent the leakage of oil while allowing for smooth rotation and movement within the equipment. The importance of oil seals cannot be overstated, as they not only ensure the efficient operation of machinery but also extend its lifespan by preventing premature wear and tear.
Oil seals are typically made from a variety of materials, including rubber,PTFE (polytetrafluoroethylene), and various metals. Each material offers unique benefits depending on the specific application and operating conditions. For instance, rubber oil seals are well-suited for applications that require flexibility and resistance to high temperatures, while PTFE seals are renowned for their chemical resistance and low friction properties.
The design of oil seals is also crucial to their performance. Factors such as the seal's geometry, material selection, and the use of additional components like springs or backup rings can significantly impact its ability to contain oil and prevent leaks. Engineers must carefully consider these factors when designing oil seals to ensure they meet the rigorous demands of industrial machinery.
One of the key challenges in the design and manufacture of oil seals is achieving a balance between sealing effectiveness and friction. While a tight seal is essential to prevent oil leakage, excessive friction can lead to increased heat generation, wear, and ultimately, failure of the seal While a tight seal is essential to prevent oil leakage, excessive friction can lead to increased heat generation, wear, and ultimately, failure of the seal
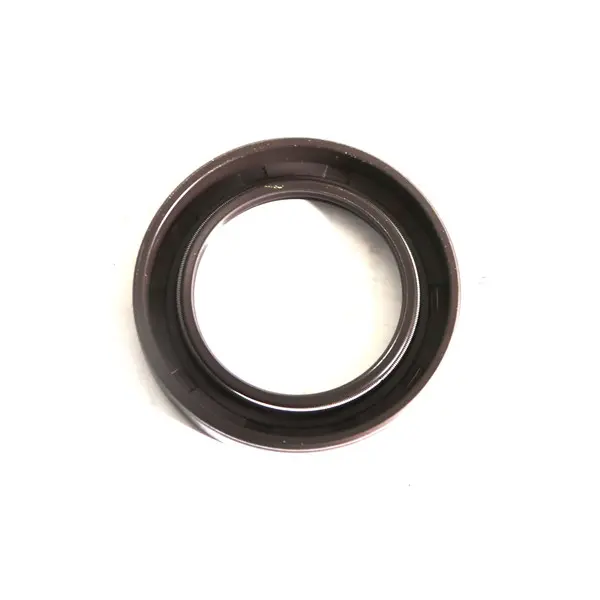
While a tight seal is essential to prevent oil leakage, excessive friction can lead to increased heat generation, wear, and ultimately, failure of the seal While a tight seal is essential to prevent oil leakage, excessive friction can lead to increased heat generation, wear, and ultimately, failure of the seal
industrial oil seals. Therefore, engineers must carefully select materials and designs that minimize friction while still providing an effective seal.
Another important consideration is the compatibility of oil seals with the oils and fluids used in the machinery. Different oils and fluids have varying properties that can affect the performance of oil seals. For example, some oils may cause swelling or degradation of the seal material, while others may accelerate wear. Therefore, it is crucial to choose oil seals that are specifically designed to work with the intended fluids.
In conclusion, industrial oil seals are indispensable components in the operation of machinery. Their ability to prevent oil leakage while allowing for smooth rotation and movement is essential to the efficient and reliable performance of industrial equipment. By carefully considering factors such as material selection, design, and compatibility with fluids, engineers can create oil seals that meet the demanding requirements of modern industry.