The Art and Science of Oil Seal Manufacturing
Oil seals play an indispensable role in various mechanical systems, acting as a barrier against the ingress of contaminants and the egress of lubricants. They are critical components in industries ranging from automotive to aerospace, ensuring efficient and smooth operation by maintaining the integrity of lubrication systems. This article delves into the intricate process of oil seal manufacturing, a blend of precision engineering, advanced materials science, and meticulous quality control.
Manufacturing oil seals begins with the selection of raw materials. High-quality rubber compounds, such as nitrile butadiene rubber (NBR) or fluoroelastomers, are commonly used due to their excellent resistance to oils and fuels. Metal components, typically steel or stainless steel, are also incorporated for reinforcement and durability. Some seals may also include PTFE (Teflon) for enhanced chemical resistance.
The manufacturing process typically starts with the creation of the rubber compound. This involves mixing the base rubber with additives like antioxidants, fillers, and accelerators to achieve the desired properties. The mixture is then cured or vulcanized, a process that transforms the soft dough into a strong, resilient material through heat and pressure.
Next comes the molding stage. The cured rubber is placed into a mold that corresponds to the specific shape of the oil seal. The mold is closed and subjected to high pressure and temperature, causing the rubber to take on the mold's shape. For seals with metal components, these are either pre-inserted into the mold or added later through a bonding process For seals with metal components, these are either pre-inserted into the mold or added later through a bonding process
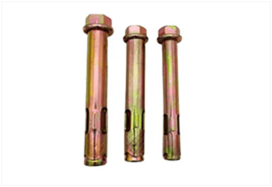
For seals with metal components, these are either pre-inserted into the mold or added later through a bonding process For seals with metal components, these are either pre-inserted into the mold or added later through a bonding process
oil seal manufacturing.
Once the seals have been molded, they undergo a series of quality checks. This includes inspecting their dimensional accuracy, surface finish, and physical properties like hardness, elasticity, and tensile strength. Any defects, however minute, can compromise the seal's performance, hence the importance of rigorous testing.
Post-production processes might involve coating the seals with lubricant to facilitate initial installation or applying anti-corrosion treatments. The final step is packaging, ensuring each seal is protected from damage during storage and transportation.
In the realm of oil seal manufacturing, innovation never ceases. New materials, designs, and production techniques are continually being explored to enhance sealing efficiency, durability, and compatibility with diverse operating conditions. The industry is also embracing sustainable practices, striving for eco-friendly materials and minimizing waste in the production process.
In conclusion, oil seal manufacturing is a complex and precise endeavor, requiring a deep understanding of materials, engineering, and quality control. It is a testament to human ingenuity and the relentless pursuit of perfection in even the smallest components that keep our machines running smoothly. From the initial mixing of raw materials to the final product, every step is critical in ensuring the reliability and longevity of oil seals in the demanding environments they serve.