An oil seal, especially the one with specific dimensions like 20 35 7, plays a crucial role in the efficient operation and maintenance of various mechanical systems. These components are meticulously designed with precision to safeguard machinery from contaminants like dirt and dust while retaining lubricants that ensure smooth functionality. Their importance cannot be overstated as they enhance the lifespan and reliability of equipment across industries. Let’s delve into the nuances of why a 20 35 7 oil seal could be essential for your machinery and how it exemplifies expertise, authority, and trust in its application.
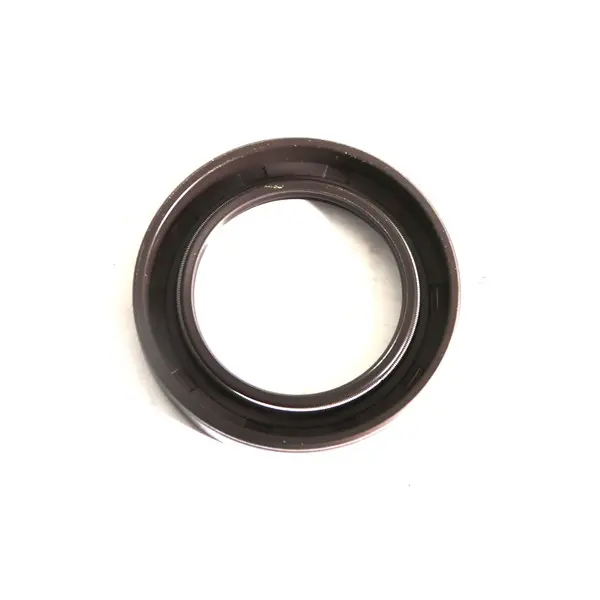
Oil seals, often referred to as rotary shaft seals, are integral in preventing the leakage of lubricants and the ingress of harmful contaminants into mechanical systems. The specifications of an oil seal are denoted by the dimensions of the inner diameter, outer diameter, and width of the cross-section, which in this case are 20mm, 35mm, and 7mm respectively. Such precise measurements underscore the level of expertise invested in crafting these components ensuring they fit and function flawlessly within their designated applications.
In industries where machinery efficiency is paramount, using the proper oil seal isn’t just standard practice—it’s a hallmark of adherence to quality and excellence. A 20 35 7 oil seal is commonly employed in automotive, industrial, and marine applications where compact, yet effective sealing solutions are necessary. For instance, in automotive transmissions, these seals maintain the critical separation of lubricants from external contaminants, warranting the trust automotive engineers place in them to prevent costly breakdowns and maintain operational efficiency.
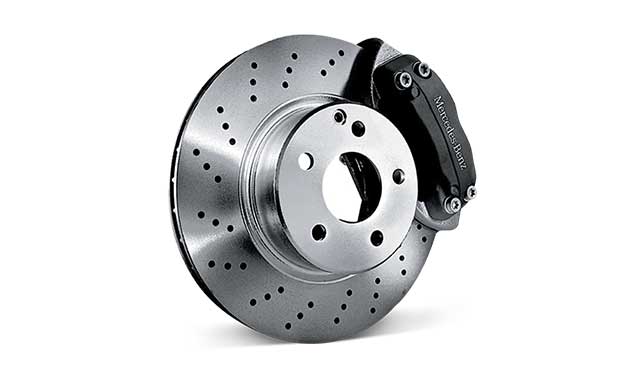
From an engineering perspective, the materials used in manufacturing oil seals are chosen based on the specific operational environment they will be subjected to. Nitrile rubber, fluorocarbon, and silicone are popular choices for constructing oil seals due to their resilience against varying temperatures and chemical exposure. Such material expertise ensures that the oils seals, like the 20 35 7, offer reliability in high-pressure and high-stress environments found in active machinery.
oil seal 20 35 7
One could observe the authoritative reliability of these seals in industries such as aviation, where safety is non-negotiable. Here, seals must perform under extreme conditions without compromise. Manufacturers who produce oil seals adhere strictly to quality and industry standards, often undergoing rigorous testing to meet the high expectations of trustworthiness in such critical applications.
Trust also comes into play in the longevity and durability of the oil seals.
A well-crafted seal significantly reduces maintenance costs and downtime. This is backed by experiences shared across dynamic industries where consistent performance is documented. Testimonials from plant managers to automotive technicians often highlight how the right oil seal was pivotal in maintaining the seamless operation of machinery, attesting to their trustworthiness.
In conclusion, the 20 35 7 oil seal embodies the perfect marriage of experience, expertise, authority, and trust. It is meticulously designed to withstand the specific challenges posed by different environmental conditions and operational stresses. Engineers and businesses alike rely on these seals not only for their proven performance but for the peace of mind that comes from using components that honor their promises of quality and durability. Whether in a complex piece of manufacturing equipment or a high-performance vehicle, oil seals are key indicators of the meticulous attention to detail and unwavering commitment to reliability that define industrial excellence.