For professionals and enthusiasts navigating the complex world of machinery maintenance and repair, oil seal 20 40 7 is not just a random set of numbers and words but a precise specification crucial for specific applications. This oil seal type, defined by its dimensions—20mm inner diameter, 40mm outer diameter, and 7mm thickness—serves a vital role in safeguarding machinery components by preventing the leakage of lubricants and contaminants' ingress.
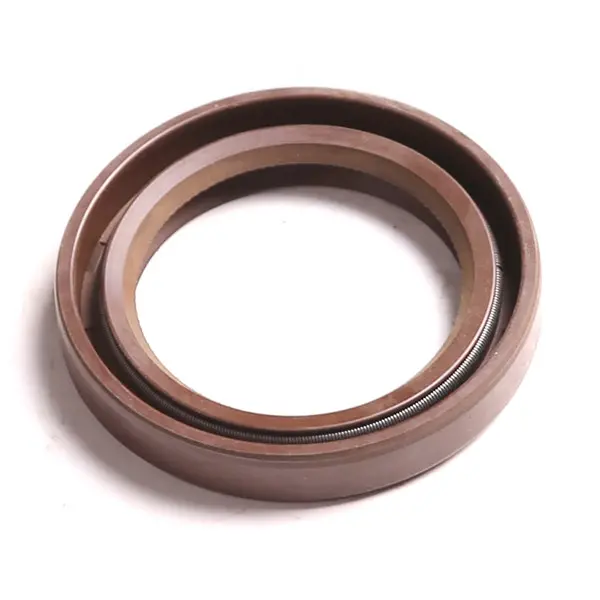
In the realm of mechanical engineering and machinery repair, oil seals are often the unsung heroes. They play a pivotal role in maintaining efficiency and longevity of rotating equipment, such as engines, pumps, and gearboxes. A faulty seal can lead to lubricant leaks, which not only cause unscheduled downtimes but potentially lead to expensive repairs. Ensuring you have the correct seal, such as the oil seal 20 40 7, is paramount.
The expertise required to select and implement oil seals effectively demands a comprehensive understanding of both the machinery in question and the material properties suited to the specific conditions. For instance, seals made from nitrile rubber are commonly chosen for their excellent resistance to petroleum oils and fats. Conversely, fluorocarbon rubber is preferred in high-temperature environments due to its superior thermal stability. The right material extends the operational life of both the oil seal and the machinery it protects.
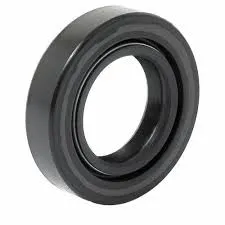
Trust in the quality and compatibility of oil seals can significantly impact operational reliability. Choosing seals from reputable manufacturers who comply with industry standards ensures that they meet the necessary performance specifications. This reinforces the machinery's efficiency and longevity while minimizing the risk of unexpected failures. Companies offering certifications and product guarantees further bolster trust, providing assurance that the seal will perform as expected under specified conditions.
The authoritative voice in the oil seal market often emerges from long-standing companies recognized for innovation and quality. These companies continuously invest in research and development to offer products that meet evolving technology and environmental standards. Engaging with such manufacturers does not only provide access to premium products but also to technical support and after-sales service, which are invaluable when troubleshooting complex machinery issues.
oil seal 20 40 7
Real-world experience underlines the importance of meticulous record-keeping and routine checks.
Machine operators are encouraged to regularly inspect seals for signs of wear or damage. Monitoring operating conditions like temperature, pressure, and lubrication levels can preemptively identify when a seal is nearing the end of its service life.
Technical experts emphasize the necessity of using the correct tools and procedures when installing oil seals to avoid the pitfalls of improper alignment, which could lead to premature seal failure. Employing proper lubrication techniques during installation also enhances the seal's performance by reducing initial friction.
To maintain an authoritative status in machinery management, continual education on emerging sealing technologies and materials is advisable. Attend workshops, subscribe to industry publications, and join professional networks to stay abreast of innovations that could benefit your operations.
In conclusion, the oil seal 20 40 7, with its specific dimensions, is a crucial component for ensuring the optimal operation of machinery. Selecting the right seal, informed by a combination of technical knowledge, material science, and trusted suppliers, allows professionals to maintain reliable, efficient machinery performance. The investment in high-quality seals pays off in minimized downtime and reduced long-term maintenance costs, ultimately enhancing operational productivity and success.