Navigating the intricate world of industrial components often brings one across the crucial, yet sometimes overlooked, component known as the oil seal. Designed with precision and intent, the oil seal 22 32 7 is engineered to serve a fundamental purpose in machinery, ensuring that fluids, particularly oil, are contained where necessary while preventing contaminants from disrupting mechanical operations.
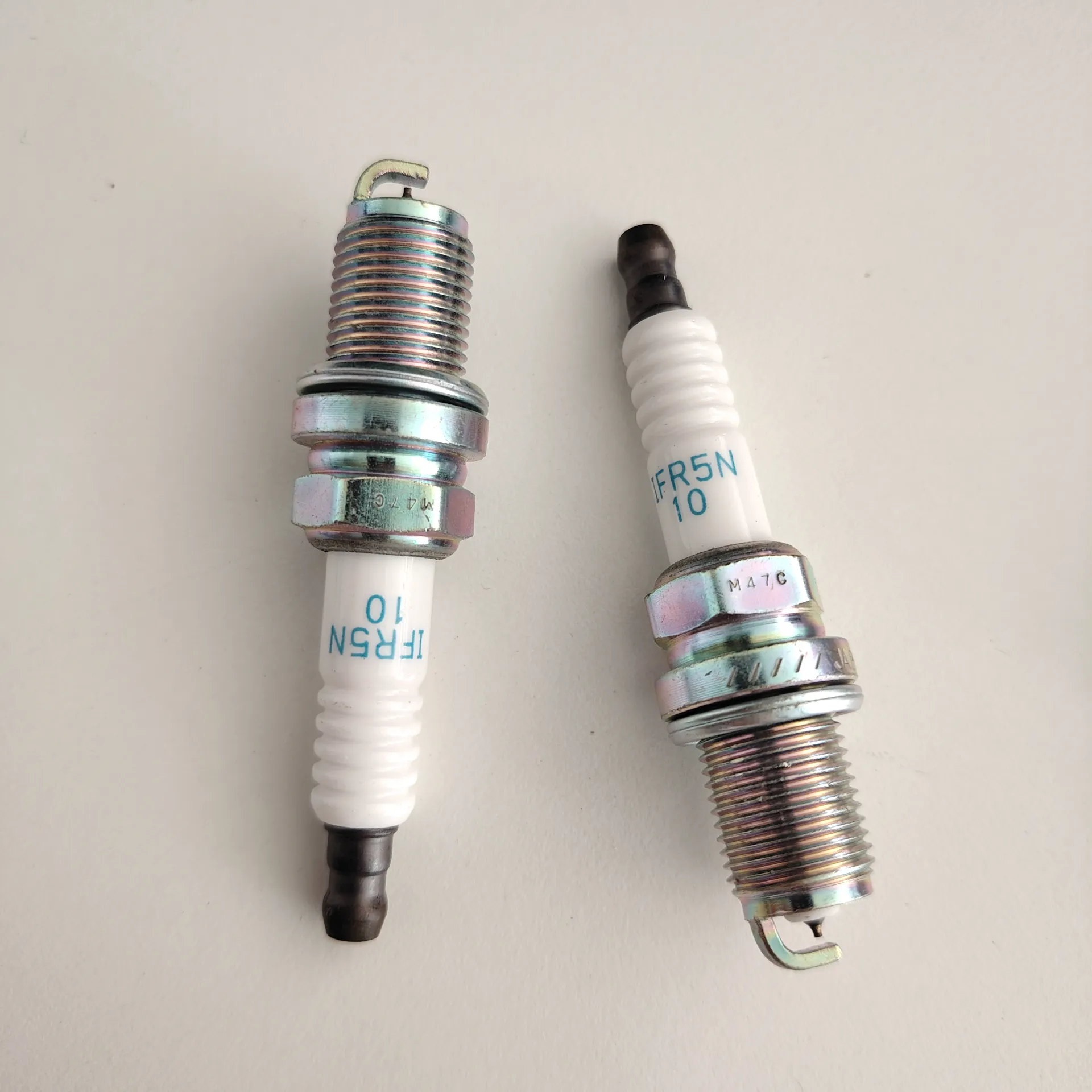
Each number in its designation speaks a language of precision 22, 32,
and 7. The first number, 22, represents the inner diameter in millimeters, a measure that ensures a snug fit over shafts of matching dimensions. This precision fit is vital for the correct functioning of machinery, avoiding any looseness that might lead to leakages or inefficiencies. In the world of mechanical engineering, where precision is king, ensuring accurate dimensions is as critical as the material of the oil seal itself.
Moving forward, the second number, 32, denotes the outer diameter. This measurement is integral to the stability of the oil seal within its housing or bore. Proper seating within its cylindrical cavity ensures that external contaminants—such as dust, water, and dirt—are kept at bay. This protective barrier is not just a line of defense; it’s a testament to the meticulous design considerations that manufacturers incorporate to safeguard the longevity and efficiency of machinery.
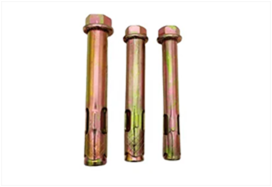
Lastly, the number 7 details the thickness of the oil seal. It might seem straightforward, but this measurement is pivotal. The thickness can influence the seal's flexibility, endurance, and its ability to adapt to shaft movement and thermal expansion. An optimized thickness ensures a balance between rugged durability and the necessary give that compensates for mechanical vibrations, heat variations, and pressure changes.
oil seal 22 32 7
An expert appreciation for the design of the oil seal 22 32 7 extends beyond its dimensional attributes. Materials play a quintessential role in determining performance. Typically composed of nitrile rubber, silicone, or fluorocarbon, the choice of material depends on the operational environment. Nitrile rubber, for instance, offers an affordable and functional solution for a range of temperatures and is resistant to many hydrocarbons. Conversely, environments that demand high-temperature resistance and oxidative stability might benefit more from silicone or fluorocarbon variants.
From an OEM (Original Equipment Manufacturer) perspective, the authority of a supplier hinges on the commitment to quality and consistency. Partnering with reputable manufacturers guarantees not only the product's reliability but also supports regulatory compliance and traceability. Companies must navigate stringent quality controls, often adhering to international standards such as ISO, to establish trust and authority in their offerings.
In bolstering trustworthiness, the performance of an oil seal in real-world applications cannot be understated. Customer testimonials often reveal insights ranging from successful integration in complex systems to commendations on the longevity and efficacy of these seals under rigorous conditions. Such testimonials not only build trust but also underscore the expertise of the product within varied industrial contexts.
Ultimately, the oil seal 22 32 7 is more than a simple component—it's a cornerstone of industrial reliability. Its strategic role in machinery underscores the broader narrative of its importance in maintaining seamless operations in sectors as diverse as automotive, manufacturing, and aerospace. While its dimensions speak to engineering precision, it's the expertise, authority, and trust established through its performance that make it an essential element in the industrial sphere.