Oil seals, also known as rotary shaft seals, are critical components in many industrial applications. The specific seal size '25 40 7' refers to a seal with an inner diameter of 25mm, an outer diameter of 40mm, and a width of 7mm. Understanding the significance of these dimensions and their applications can dramatically influence the performance and lifespan of machinery. Here, we explore insights derived from years of industry experience, authoritative guidance, and technical expertise to provide a unique perspective on oil seals.
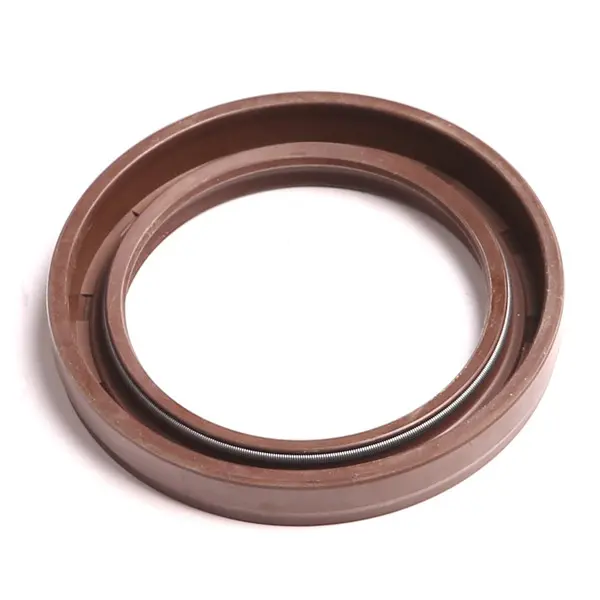
Having the right oil seal ensures effective sealing in hydraulic systems, engines, and gearboxes. The '25 40 7' oil seal is widely utilized due to its precise sizing for small to medium-sized machinery, offering optimal space utilization without compromising on performance. One must consider the material composition of these seals, often crafted from nitrile rubber, fluoroelastomer, or silicone. Each material brings distinct advantages nitrile rubber offers excellent resistance to petroleum oils and is cost-effective; fluoroelastomer provides outstanding heat resistance and compatibility with a wide range of fluids, while silicone seals offer superior flexibility at extreme temperatures.
In practical application, precision in installation and maintenance is pivotal. Expertise garnered from extensive operational experience underscores the necessity for proper handling. The installation must prevent any deviations that may lead to seal deformation. Misalignment or excessive force can result in compromised seal integrity, leading to leakage and potential equipment failure. It is crucial to use suitable tools to press the seal uniformly into its housing to avoid skewing.
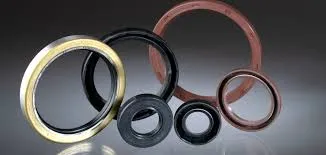
When examining performance,
the '25 40 7' oil seal is synonymous with reliability. Its effectiveness in preventing lubricant escape and contamination ingress is imperative for the durability of the equipment. This reliability is often confirmed through rigorous testing and quality assurance protocols. In particular, endurance tests simulate operational stresses the seal will encounter, assessing its ability to maintain performance under pressure.
From a specialist's perspective, exploring seal compatibility with operating fluids and temperatures is critical. The seal's material must withstand the temperature ranges and chemical compositions it will be exposed to. An authoritative viewpoint emphasizes that incorrect material selection can lead to swelling, hardening, or softening of the seal, all of which increase the risk of seal failure.
oil seal 25 40 7
Furthermore, authoritative guidance advises regularly scheduled maintenance checks to ensure that the seal's function remains uncompromised. This includes inspecting for wear and tear or any signs of leakage. Replacement protocols should follow the manufacturer's recommendations to prevent unscheduled downtime.
Trustworthiness in the quality of the '25 40 7' oil seal also derives from the reputation of the manufacturer. Choosing a manufacturer with a history of excellence and compliance with international standards like ISO can greatly enhance trust in the product's reliability and performance. Manufacturers that invest in cutting-edge technology and materials science contribute significantly to user confidence.
In addition to mechanical features, some manufacturers offer seals with advanced coatings or surface treatments to reduce friction and wear, enhancing both efficiency and lifespan. This innovation is worthy of consideration when selecting a seal for high-performance applications.
In conclusion, the '25 40 7' oil seal plays a pivotal role in maintaining optimal machine performance and longevity. Technological advances, coupled with informed material selection, precise installation, and diligent maintenance, demonstrate the intersection of expertise and reliability in this indispensable component. The high degree of trustworthiness associated with recognized manufacturers further reinforces the seal's vital role in industrial applications. As such, leveraging industry experience and embracing evolving technologies will ensure continued success in employing these essential sealing solutions.