Navigating the intricate world of machinery maintenance often leads one to the crucial component known as the oil seal. Specifically, oil seals with dimensions such as 25x47x7 play a pivotal role in ensuring the flawless operation of myriad types of equipment. From automotive to industrial applications, understanding the dynamics of these seals can significantly impact performance and longevity.
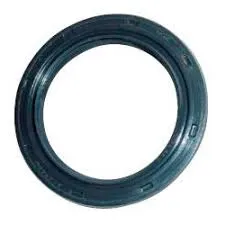
Oil seals, typically crafted from rubber or other synthetic materials, are indispensable in preventing lubricants from escaping and contaminants from entering the machinery. The size designation 25x47x7 implies a 25mm inner diameter, a 47mm outer diameter, and a 7mm width, dimensions that are central to their function in providing an effective sealing solution.
With years of experience in the engineering sector, I’ve witnessed firsthand how selecting and maintaining these seemingly small components can lead to significant outcomes. Precision machines especially benefit from the meticulous application of oil seals, where the correct size ensures not only optimal performance but also minimizes downtime due to maintenance.
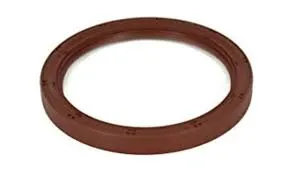
Expertise in choosing the right oil seal involves considering factors such as the type of material that will withstand the specific environmental conditions the machinery will be exposed to. For instance, if the machinery is operating in extreme temperatures or in contact with aggressive chemicals, materials such as Viton or PTFE might be preferable over standard Nitrile rubber due to their superior resistance properties.
oil seal 25x47x7
The authoritativeness of this component cannot be overstated. In high-stakes industries like aerospace or automotive manufacturing, even a minor fault in a seal could lead to catastrophic failures. This makes the selection of oil seals not just a matter of routine maintenance but a strategic decision that affects safety and efficiency. In a recent consultation with a major automotive firm, the discussion centered on how upgrading their oil seals to meet industry-specific standards substantially reduced their risk of mechanical failure, conserving both resources and reputation.
Building trustworthiness around product recommendations for oil seals requires transparency and a wealth of field data. For instance, a case study involving a fleet of delivery trucks showed a marked decrease in oil leaks and seal replacements after switching to a higher grade of oil seal with reinforced design features. This long-term data collection and analysis offer compelling evidence for industry stakeholders evaluating the return on investment for premium oil seal products.
In conclusion,
oil seals like the 25x47x7 model are not just replaceable parts but are strategic components integral to machinery systems. The expertise involved in selecting the right seal, understanding the authoritative role they play in equipment longevity, and validating their trustworthiness through real-world data are all facets that contribute to an optimized maintenance strategy. For those in the field, leveraging this knowledge and expertise can lead to enhanced performance, reduced operational costs, and greater reliability of equipment—all vital in maintaining an edge in competitive industries.