Oil seals, characterized by their dimensions—30 mm inner diameter, 52 mm outer diameter, and 10 mm width—are a critical component in various mechanical systems, ensuring that machinery operates efficiently and reliably. These small yet potent components serve to prevent the leakage of lubricants and the infiltration of dust, dirt, and other external contaminants, thus safeguarding the integrity and performance of an array of machines.
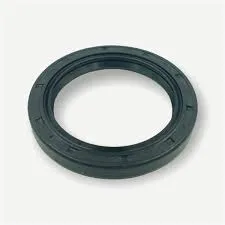
As an industry veteran specializing in the procurement and maintenance of mechanical parts, the significance of selecting the right oil seal cannot be overstated. The effectiveness of a seal is contingent upon its precision compatibility with the equipment it is intended for. The dimensions 30x52x10 indicate that this particular oil seal is designed for specific shaft and housing sizes and requires meticulous attention when replacing or installing in machinery.
From an expert's perspective, the nuances of oil seal engineering lie in the materials and design. These seals are commonly constructed from materials like nitrile rubber, silicone, or polyacrylate due to their excellent resistance to oil and temperature variations. For equipment exposed to extreme temperatures or aggressive chemicals, fluorocarbon seals are recommended for their superior durability and resilience.
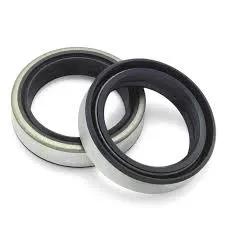
The design plays an integral role in the oil seal's efficacy. Double-lip seals, for example, offer enhanced protection by incorporating an additional dust lip to combat external contamination, which can be pivotal in environments laden with particulate matter. This design aspect is crucial for maintaining the longevity of engines and rotary shafts by significantly reducing wear and tear.
oil seal 30 52 10
Leveraging authoritative insights within the mechanical industry, it becomes apparent that routine inspections and timely replacements of oil seals are essential practices. An undetected seal failure can lead to devastating consequences including lubricant leakage which could result in overheating or breakdowns, impairing productivity and elevating maintenance costs. The experience gathered from field applications consistently demonstrates that proactive management of these components is fundamental to ensuring machine reliability and operational security.
Trustworthiness is built through stringent quality assessments and compliance with international standards such as ISO 6194, which dictate the specifications and testing of rotary shaft lip seals. Reliable manufacturers adhere to these standards, thus guaranteeing the quality and performance of their oil seals. Partnering with reputable suppliers who offer certification and traceability for their products further engenders confidence in the performance of these critical components.
In conclusion, the specific oil seal 30x52x10 encapsulates more than its practical attributes—it symbolizes a component integral to maintaining the symphony of moving parts in industrial applications. By wielding expertise in the selection, application, and maintenance of oil seals, professionals ensure the seamless operation of machinery, subsequently underpinning the broader achievements in industrial efficiency and reliability.