In the world of machinery and engineering, the importance of components like oil seals cannot be overstated. An oil seal 40 52 7 is a critical part of various machines, designed to protect bearings and shafts by preventing lubricant leakage and keeping contaminants out. Through concrete experience and knowledge, understanding the specifications, applications, and maintenance of these components is key to optimizing their performance and longevity.

Firstly, let’s delve into the specifics the numbers 40 52 7 refer to the dimensions of the oil seal in millimeters. The first number, 40, indicates the inner diameter that fits snugly around the shaft. The second number, 52, is the outer diameter which aligns with the housing, and the last, 7, designates the thickness or width of the seal. These dimensions are crucial for ensuring a proper fit, which is paramount for the seal to function effectively. Any deviation from these measurements can compromise its ability to maintain the intended barrier, leading to potential system failures.
With years of experience in the field, many professionals know that selecting the right material for an oil seal is just as important as its dimensions. Common materials include nitrile rubber, silicone, and Viton, each offering unique benefits. For example, nitrile rubber is often favored for its excellent resistance to oil and good wear performance, making it suitable for general purpose sealing. Silicone seals are used in applications with extreme temperature variations, while Viton is known for its chemical resistance in hostile environments. Choosing the correct material is based on the operating conditions, ensuring efficiency and preventing premature failure.
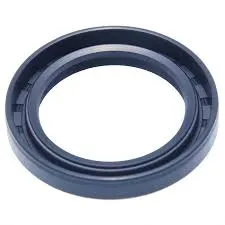
In terms of expertise, the proper installation of an oil seal 40 52 7 plays a significant role in its effectiveness. Experts recommend thoroughly cleaning the mating surfaces before installation to remove any debris or old lubricant residue. Lubricating the seal lip lightly can aid in reducing friction and heat during the initial operation, promoting a longer service life. During installation, applying an even pressure is crucial to avoid warping and to ensure a uniform fit. Specialized tools designed for seal installation can aid in achieving perfect alignment and pressure.
oil seal 40 52 7
The authoritativeness of information within this field is often reaffirmed through industry standards and guidelines. Many oil seal manufacturers adhere to standards set by organizations such as the Society of Automotive Engineers (SAE) and the International Organization for Standardization (ISO). These standards ensure that seals are manufactured to meet exceptional quality and performance criteria. It’s vital for businesses and consumers to seek products that comply with these standards to ensure reliability and efficiency in their applications.
Trustworthiness, a cornerstone of product selection, is built through the demonstrable track record of oil seals in various applications. Real-world performance data and customer testimonials work hand-in-hand to build confidence in these small yet significant components. A seal that consistently performs over its expected lifespan without leakage or failure reinforces its reliability. Comprehensive warranty policies further enhance consumer trust, providing assurance in the manufacturer's commitment to quality.
Moreover,
the versatility of oil seals extends beyond just machinery. They find applications in automotive sectors, aerospace, marine, agricultural equipment, and many other fields. Each sector demands specific attributes from the oil seals, reaffirming the need for a thorough understanding and careful selection based on the operational environment. Whether it’s the high RPMs of a car engine or the aggressive conditions faced by agricultural machinery, selecting an appropriately sized seal like the oil seal 40 52 7 is integral to the seamless operation of these machines.
In conclusion, the oil seal 40 52 7 is more than just a component; it’s a critical guardian of mechanical integrity. Ensuring its correct size, material, and installation leads to enhanced machine performance and longevity. By adhering to industry standards and trusting in proven products, industries worldwide continue to rely on these seals to keep their operations running smoothly, underlining their unwavering importance in modern engineering and technology-driven environments.