Navigating the intricate world of machinery maintenance often brings us to the small yet powerful component known as the oil seal. Specific sizes, such as the oil seal 40 62 10, play a vital role in ensuring mechanical systems run smoothly and efficiently. Understanding the significance, functionality, and quality selection of these oil seals is crucial for engineers, mechanics, and industry stakeholders alike.

Oil seals are designed to keep lubricants in and contaminants out, ensuring that machines operate efficiently. The numbers 40 62 10 refer to specific dimensions—40mm for the inner diameter, 62mm for the outer diameter, and 10mm for the width. These parameters are critical in ensuring the proper fit and function within various mechanical systems. Precision in size directly translates to effectiveness in performance, reducing the risk of leakage and parts contamination.
The choice of material in manufacturing oil seals like the 40 62 10 is of paramount importance. Common materials include nitrile rubber (NBR), fluorocarbon rubber (FKM), and polyacrylate, each offering unique benefits. NBR is known for its excellent resistance to petroleum-based oils and good balance of performance characteristics. FKM offers superior heat resistance, making it suitable for high-temperature applications, while polyacrylate is preferred for its resilience against oxidation and aging. Selecting the right material depends on the operating environment and the specific requirements of the machinery.
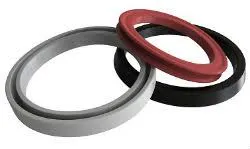
Installation of an oil seal is a precise endeavor that requires attention to detail and technical expertise. A misaligned seal or incorrect installation can lead to premature failure, which necessitates costly repairs and downtime. Therefore, proper training and adherence to installation guidelines are crucial. It’s recommended to use specialized tools to avoid deforming the seal during installation, ensuring it seats correctly onto the shaft.
Regular maintenance checks and monitoring are integral in prolonging the life of oil seals. Scheduled inspections help identify wear and tear before it escalates into more significant issues. The inclusion of a consistent lubrication regime further enhances the durability of the seals, reducing friction and heat generation in high-speed applications. In harsh environments, additional protection mechanisms such as dust boots or protective covers can further extend the service life of oil seals.
oil seal 40 62 10
The stakes in choosing the correct oil seal extend beyond mechanical performance—they affect the economical aspects of a business. Effective sealing solutions lead to improved energy efficiency, reduced lubricant consumption, and minimized environmental impact. A well-maintained oil seal translates to fewer breakdowns, lesser maintenance costs, and increased machinery lifespan, ensuring seamless operation and optimal productivity.
Furthermore, the credibility of a supplier plays a pivotal role in the procurement of high-quality oil seals. Reputable manufacturers provide comprehensive data sheets, offering insights into material specifications, temperature ranges, and compatibility considerations. Engaging with suppliers who hold certifications such as ISO standards adds an additional layer of assurance regarding the quality and reliability of the oil seals.
In the ever-evolving landscape of industrial machinery, staying updated with advancements in seal technology can offer a competitive edge. Innovations in composite materials and sealing configurations are paving the way for enhanced performance, offering solutions that cater to more demanding applications with higher efficiency.
Professionals focused on enhancing mechanical sustainability must consider oil seals as fundamental components. Beyond their simple appearance, components like the oil seal 40 62 10 embody engineering precision and expertise. By prioritizing quality, proper installation, and regular maintenance, industries can leverage these vital parts not only to augment machine reliability but to achieve broader business and environmental goals.