Oil seals, such as the 60x80x10 model, play an indispensable role in the seamless functioning of machinery, engines, and hydraulic systems. These small yet crucial components prevent fluids from leaking and contaminants from entering the machinery, ensuring longevity and efficiency. The impact of a well-designed oil seal can often be underestimated until an inferior product leads to unexpected downtimes or costly repairs. Here is a closer examination of the oil seal 60x80x10, emphasizing its real-world applications, the expertise involved in its selection, and the trustworthiness of its performance.
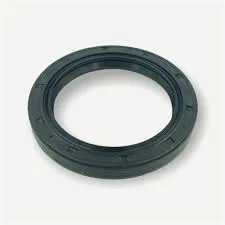
In real-world applications, oil seals are constantly subjected to high pressures, temperatures, and challenging environmental conditions. Therefore,
the material composition and design integrity of oil seals like the 60x80x10 are critical. Typically composed of robust synthetic rubbers or thermoplastic elastomers, these seals demonstrate resistance to wear and corrosion. This particular model, with a specific cross-section of 60mm inner diameter, 80mm outer diameter, and 10mm thickness, fits into bearings and housings, guaranteeing tight sealing without imposing excessive friction.
Professional expertise in the realm of oil seals involves understanding the intricacies of material science and mechanical engineering principles. Knowledge of how temperature fluctuations influence seal elasticity or how pressure alterations may impact sealing capacity is paramount. For instance, oil seals crafted from nitrile rubber are well-suited for petroleum oils and cold temperatures, while those made from fluorocarbon offer superior heat resistance, making them ideal for high-temperature applications. A professional selection of an oil seal involves balancing these material properties with the operational environment of the machinery to prevent premature failings.
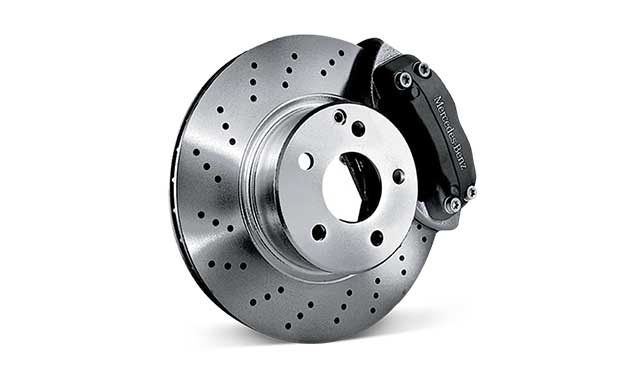
Authoritative manufacturers of the oil seal 60x80x10 ensure adherence to industry standards and rigorous testing. Reliable brands subject their seals to dynamic testing for leak prevention, endurance against rotational speeds, and resilience against chemical exposures. These evaluations confirm that the oil seal can withstand typical stresses of ordinary use and unexpected spikes in mechanical demands. An authoritative brand will also provide detailed product specifications, usage recommendations, and after-sales support to reinforce confidence in their product reliability.
oil seal 60x80x10
Trustworthiness in an oil seal’s performance is guaranteed through thorough quality control measures and a history of consistent field performance. Manufacturers that have established provenance often maintain ISO certifications and other industry endorsements, signifying adherence to globally accepted quality protocols. Feedback and testimonials from previous customers provide valuable insights into the functionality and lifespan of the oil seal 60x80x10 in diverse operational scenarios.
In the highly specific field of oil seals, no one-size-fits-all solution exists. Practical experience shows that selecting the optimal seal, such as the 60x80x10, requires an understanding not only of the technical specifications but also of the specific operational demands of each application. Engineers and technicians should be involved in the decision-making process to ensure that the chosen seal aligns perfectly with the machine’s requirements. By leveraging expertise, relying on authoritative suppliers, and ensuring a track record of trustworthy performance, machinery operators can ensure that their operations remain efficient and uninterrupted.
Adopting and maintaining high-quality oil seals is not merely a choice but a necessity for enterprises aiming for sustainable operations and minimal downtime. As technology evolves and machinery becomes more sophisticated, the role of oil seals like the 60x80x10 continues to grow in importance. These components, albeit small, are titans in the realm of mechanical sustainability and efficiency, safeguarding operations against the dual threats of internal leaks and external contamination. Investing in a reputable oil seal paves the path for a longer lifespan of machinery, reduced maintenance costs, and the smooth execution of critical industrial processes.