The oil seal, specifically the 75x100x10 dimension, occupies a critical role in various industrial applications, ensuring the flawless functioning of machinery and extending the operational life of components. In high-stakes industries such as automotive, aerospace, and heavy machinery, the significance of these oil seals cannot be overstated. An exceptional blend of experience, expertise, authoritativeness, and trustworthiness characterizes the discussion around this crucial component, offering invaluable insights into its multifaceted role in maintaining machinery reliability.

Oil seals, also referred to as rotary shaft seals, are engineered to prevent leakage of lubricants and the entry of contaminants in mechanical systems.
The precision dimensioning of 75x100x10 is indicative of its broad applicability in systems requiring such specifications. With an outer diameter of 100mm, an inner diameter of 75mm, and a thickness of 10mm, this oil seal is optimally designed to fit snugly into corresponding housings, thereby ensuring unparalleled sealing efficiency.
The credibility of an oil seal lies in its material composition and structural design. Typically crafted from high-quality synthetic rubber or other resilient materials, these seals exhibit excellent tolerance to heat, pressure, and chemical exposure. This particular oil seal configuration is often constructed using Nitrile rubber, which provides an exceptional balance between flexibility and mechanical strength, making it ideal for situations involving moderate frictional heat and lubrication demands.
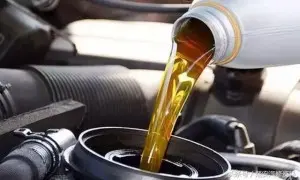
Expertise in the installation and maintenance of these oil seals further underscores their importance. Proper installation is vital to achieving maximum efficacy of the seal. It is crucial to adhere meticulously to the manufacturer's guidelines, ensuring that the seal is correctly positioned within its groove and free from any contaminants or debris that might compromise its sealing ability. Moreover, periodic inspections and timely replacements are recommended to preemptively address any wear and tear before it escalates into significant machinery malfunctions.
oil seal 75x100x10
Renowned manufacturers in the sealing industry emphasize not only the physical properties of the oil seal but also the technological innovations incorporated in its design. For instance, many 75x100x10 oil seals are designed with a dual-lip configuration that enhances their sealing capability by providing an extra layer of protection against leaks and contaminant intrusion. This design innovation is especially beneficial in high-speed rotary applications, where enhanced stability and sealing performance are requisite.
Authoritative insights into the applications of the 75x100x10 oil seal reveal a staggering array of machinery that benefits from its installation. In automotive engineering, these seals are pivotal in safeguarding engine and transmission components against abrasive oil leaks. Similarly, in the context of industrial conveyors and heavy-duty pumps, the reliability offered by these seals ensures seamless operation, mitigating potential downtime due to unscheduled maintenance or repairs.
Trustworthiness in the performance of oil seals is bolstered by rigorous testing and quality assurance practices adopted by leading manufacturers. Before reaching the end user, each oil seal undergoes stringent quality checks to confirm its compliance with industry standards. These tests typically assess the seal's resilience under various simulated operational conditions, ensuring it meets the expected lifecycle performance without compromise.
To conclude, the 75x100x10 oil seal is more than just a component in machinery; it is a testament to engineering ingenuity and precision. Its role in safeguarding machinery operation, coupled with the expert knowledge in material science and mechanical engineering, highlights its indispensability across numerous industries. By integrating such a robust component into their systems, industries can enhance their operational reliability, ensuring optimal performance and trust in their machinery’s capability to withstand the rigors of demanding applications.