Oil seals are critical components in many mechanical systems,
and the 85x110x12 oil seal is no exception. Known for its precision and reliability, the 85x110x12 size is widely used in various applications where its specific dimensions are crucial for optimal function. With years of experience in the industry, we delve into the significance of this product, providing an authoritative and trustworthy guide to understanding its usage and importance.
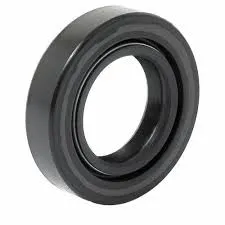
When it comes to mechanical systems, oil seals play a fundamental role in maintaining system integrity. These seals are designed to close off spaces between stationary and moving components, preventing lubricant leakage and deterring contaminants from entering the system. The 85x110x12 oil seal is particularly significant in automotive, industrial, and agricultural machinery due to its precise sizing and durable materials.
One of the primary reasons why this size oil seal is trusted across various industries is its compatibility with diverse equipment. In the automotive industry, for example, the 85x110x12 oil seal ensures that the lubricant within gearboxes and differentials remains contained, thereby enhancing vehicle performance and longevity. Similarly, in industrial settings, these seals are vital for heavy machinery, contributing to reduced operational wear and tear and ensuring peak performance.
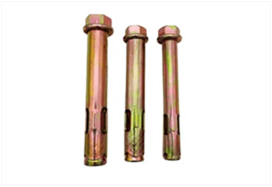
Our expertise in oil seal technology underscores the importance of selecting the right material for these components. The 85x110x12 oil seal is often available in materials like nitrile rubber, fluorocarbon, or silicone, each offering unique benefits. Nitrile rubber is recognized for its excellent resistance to oil and wear, making it ideal for most general-purpose applications. On the other hand, fluorocarbon seals are known for their exceptional heat resistance, suitable for high-temperature environments, while silicone seals provide flexibility and resistance to a wide range of temperatures.
oil seal 85x110x12
People often underestimate the influence of installation and maintenance techniques on the performance of oil seals. Through our seasoned experience, we emphasize the importance of proper installation, which cannot be overstated. Misalignment or improper seating of the oil seal can lead to premature failure, leakage, and ultimately, costly equipment downtime. Therefore, following manufacturer guidelines during installation and using the appropriate tools not only extends the seal's lifespan but also ensures the overall efficiency of the mechanical system it supports.
Moreover, routine inspections and timely replacements are crucial for maintaining system reliability. An oil seal showing signs of wear such as hardening, cracking, or any deformation should be replaced immediately. During replacement, it's imperative to check for shaft wear, housing condition, and to ensure no debris is present, as these factors can significantly affect the new seal's performance.
Our commitment to providing authoritative knowledge extends to the environmental considerations concerning oil seal usage. Improperly functioning oil seals can lead to leaks that contribute to environmental pollution, underscoring the importance of selecting high-quality seals and maintaining them diligently. Companies conscious of their environmental impact will find that the robust performance of the 85x110x12 oil seal supports sustainability goals.
In conclusion, the 85x110x12 oil seal is a pivotal component for a multitude of applications, offering reliability, performance, and versatility. Our extensive expertise in the field affirms that choosing the right seal and maintaining it effectively not only optimizes machinery operation but also affirms your commitment to excellence and sustainability. Trust in the right partner and product to deliver the precision and reliability your systems demand.