Oil seal dimensions play a crucial role in ensuring the optimal performance and reliability of machinery across various industries. Their proper sizing is fundamental to maintaining the longevity of mechanical systems by preventing the ingress of contaminants and the escape of lubricants. For professionals involved in equipment maintenance and design, understanding the nuances of oil seal dimensions is paramount.
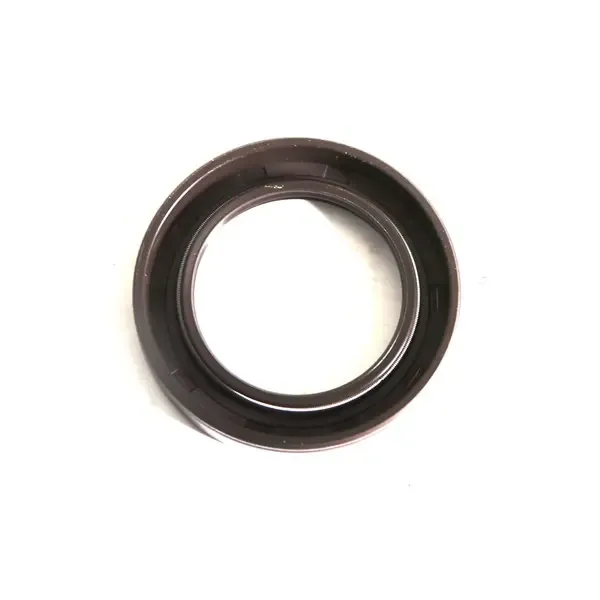
The key to choosing the correct oil seal dimensions starts with familiarizing oneself with the specific requirements of the application. Different machinery and environments impose unique demands on oil seals, impacting their size and material selection. For instance, automotive applications typically demand seals that can withstand high temperatures and pressures, whereas those used in agricultural equipment may require resistance to dirt and moisture. This specificity underlines the importance of expertise in selecting the appropriate dimensions.
Another essential factor influencing oil seal dimensions is the type of seal. The most common types include rotary shaft seals, hydraulic seals, and pneumatic seals. Each type operates under different conditions and therefore requires specialized consideration regarding dimension. Rotary shaft seals, for example, must accommodate the shaft’s specific diameter while also accounting for dynamic movements. On the contrary, hydraulic seals must manage fluid pressure without leaking, demanding precise fitting within hydraulic systems.

Dimensions are not merely about fitting the seal into the housing; they also involve ensuring a snug fit on the shaft or bore. The inside diameter (ID) should typically align closely with the shaft’s diameter to prevent slip and wear, while the outside diameter (OD) ensures a tight fit within the housing. A small deviation in these dimensions could lead to leaks or premature wear, leading to system failures. Therefore, the precision in measurement and adherence to standardized dimensions cannot be overstated.
oil seal dimension
Material selection also heavily influences the dimensions. Rubber, PTFE, and metal are common materials used in oil seal construction, each with its tolerance levels and dimensional stability under varying temperatures and pressures. For example, rubber seals may expand or contract slightly under temperature changes, which may require slight dimension adjustments during design. Understanding these properties is essential for engineers and designers to ensure that the selected seal maintains its integrity throughout its service life.
An often overlooked aspect is the importance of surface finish and hardness of the shaft and housing, which correlates directly with the seal against which it must accommodate. Even the best-sealed dimension will fail if the surface it mates with is not of compatible hardness or has an inappropriate finish. A higher finish with the correct roughness average (Ra) can improve the seal's efficiency and extend its lifespan, emphasizing the importance of considering the overall system design and condition during selection.
Industry standards such as ISO and DIN provide guidance on standard dimensions and material specifications, ensuring compatibility and interchangeability across different regions and manufacturers. Adhering to these standards not only improves reliability but also enhances trustworthiness in the product choice, as these standards have been tested for performance consistency in various operating conditions. Thus, being informed about these standards is not merely a recommendation but a necessity for achieving excellence in equipment reliability.
Ultimately, the importance of selecting the right oil seal dimensions cannot be overstated. It involves a detailed understanding of the machine's environment, seal type, material characteristics, and adherence to industry standards. By leveraging expertise, professionals can make informed decisions, ensuring optimal performance and longevity of machinery. For anyone involved in the design, maintenance, or operation of machinery, mastering the intricacies of oil seal dimensions is a crucial step in enhancing the efficiency and reliability of mechanical systems.