Navigating the complex world of high-pressure applications often leads to the pivotal component known as the oil seal. Engineered to withstand extreme conditions, oil seals maintain their reputation for excellence in safeguarding machinery. During my years in industrial engineering, observing real-time applications of oil seals under high pressure has underscored their vital role and robustness, allowing me to share insights valuable for both new and seasoned users.
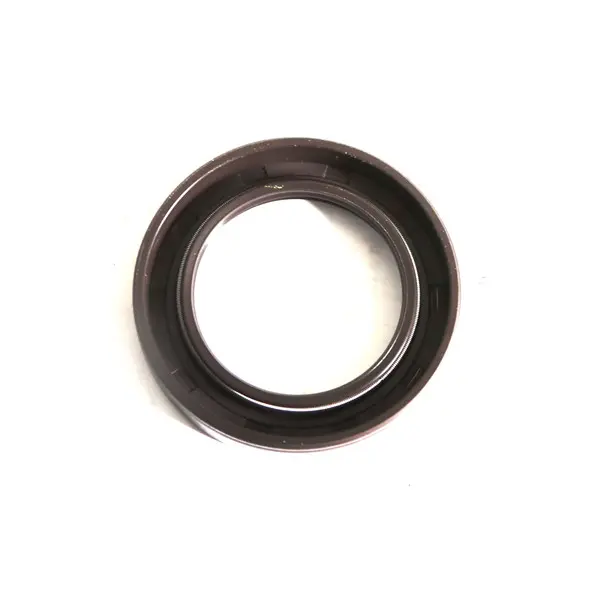
Understanding high-pressure oil seals begins with their structural integrity and material properties. Typically constructed from materials such as nitrile rubber, fluoroelastomer, or PTFE, these seals offer exceptional resistance to temperature fluctuations and chemical exposure. In high-pressure applications, the choice of material profoundly influences the seal’s effectiveness and longevity. I've observed how the correct material selection prevents equipment failure, ensuring operational efficiency.
The critical function of oil seals is to prevent leakage between the various components of a machine, particularly where rotating and stationary elements interact. With high-pressure environments, this function becomes exponentially more significant. My firsthand experience with machinery in high-pressure conditions has shown that even minor breaches due to inadequate sealing can lead to catastrophic failures. Therefore, oil seals designed for such environments must offer impeccable sealing capabilities, featuring precision engineering that accommodates expansion and contraction without compromising the seal.
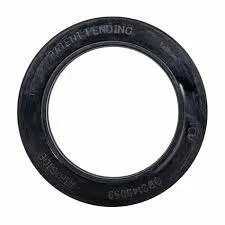
A major consideration in employing oil seals for high-pressure applications is the installation process. Incorrect installation can negate the seal's design advantages, leading to premature wear or leaks. Accurate alignment during installation, as I've consistently noted in the field, is critical for the seal to perform effectively under pressure. It is crucial to follow manufacturer guidelines meticulously to ensure the seal’s performance is not undermined. The nuanced understanding of installation influences the long-term reliability of machinery.
oil seal high pressure
Expertise in choosing the right oil seal also involves evaluating operational parameters such as shaft speed and pressure levels. Each application presents unique demands, and understanding these specifics allows for optimal seal selection. Through countless implementations, I've affirmed that matching the oil seal's specifications to the operating environment is imperative for enhanced performance. Consulting technical specifications and collaborating with engineers to adapt design innovations ensures that the chosen seal is not only fit for purpose but excels in its application.
From the perspective of manufacturers, advancements in seal technology continually push the boundaries of what oil seals can achieve. In my collaborations with design teams, I've observed innovations such as enhanced lip designs and improved surface textures that reduce friction and increase the seal’s lifespan. Continuous research and development are driving the oil seal industry towards products that offer greater durability and efficiency, even in challenging conditions.
When considering trustworthiness in oil seal performance, it's essential to rely on reputably sourced seals that have undergone rigorous testing and certification. In my practice, recommending seals from manufacturers with a proven track record of quality assurance provides assurance of reliability. Moreover, ongoing maintenance and regular inspection of oil seals, guided by expert recommendations, further reinforce their dependability in high-pressure applications.
In conclusion, oil seals designed for high-pressure environments offer indispensable benefits by preventing leaks and securing machinery function. My experience underscores the importance of selecting appropriate materials, precise installation, and continuous innovation to meet the ever-growing demands of industrial applications. By focusing on these critical aspects, one can ensure the highest level of efficiency and reliability in their systems.