In the intricate world of industrial machinery, oil seals designed for high-pressure environments stand as unsung heroes, ensuring operational integrity and longevity. Engineered with precision, these seals play a pivotal role in maintaining the efficiency of various mechanical systems, making them indispensable across multiple sectors.

Oil seals, often made from advanced elastomers or polymer materials, are specifically designed to endure extreme conditions. Their primary role is to prevent leakage and contamination, safeguarding the lubricant within the machinery while simultaneously keeping harmful particles out. The significance of high-pressure oil seals cannot be understated as they operate in demanding environments where malfunction could lead to costly downtime or catastrophic equipment failure.
Industrial experts emphasize the importance of understanding the specific requirements of each application when choosing an oil seal. The seal's material composition is crucial, with choices depending on factors like temperature range, chemical exposure, and the nature of the fluids involved. Nitrile rubber (NBR), for instance, is cost-effective and widely used for general purposes, whereas fluorocarbon rubber (FKM) is preferred for high-temperature and aggressive chemical conditions.
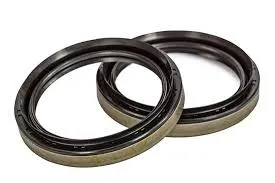
Moreover, the construction of these seals is not one-size-fits-all. Depending on the pressure and environment, they may be designed with features such as double lips, metallic reinforcements, or spring-loaded elements to enhance sealing efficiency. Such adaptable designs ensure that the seals provide robust performance, even when dealing with extreme pressures in hydraulic systems or automotive transmissions.
From a reliability standpoint, manufacturers invest heavily in research and development to innovate new synthetic materials and design enhancements. This continuous evolution not only extends the life of the seals but also amplifies their performance in reducing friction and wear. Leading companies in the sector often collaborate with industry experts to refine their products, keeping pace with technological advancements and industrial demands.
oil seal high pressure
The expertise surrounding high-pressure oil seals extends beyond just production. Professionals in the field are also highly skilled in predictive maintenance practices. They understand that despite high-quality materials and designs, regular inspection and timely replacement of seals are vital to prevent abrasive wear and inevitable failure. Informed by empirical data and field experience, these maintenance strategies are integral to optimizing machinery life cycle costs and enhancing overall system reliability.
Authoritative insights from industry pioneers also point towards the growing trend of integrating digital technologies with oil seal applications. Smart sensors and monitoring systems aid in predictive diagnostics, allowing for real-time condition monitoring. This technological leap forwards, supported by experts in industrial IoT, ensures that any potential issues with seals can be detected and remedied promptly, thereby fortifying trust and operational security.
Ultimately, the credibility of any high-pressure oil seal lies in its proven track record across diverse applications. Whether in automotive, aerospace, or heavy machinery sectors, users seek products backed by empirical performance data and positive industry testimonials. For a product to be truly trustworthy, transparency in testing standards and certifications becomes crucial, reassuring users of its credibility and reliability.
In conclusion,
the role of oil seals in high-pressure environments transcends their physical application. They encapsulate years of engineering excellence, expertise, and industry integration. By continuously pushing boundaries through innovation and robust testing, they stand as a testament to human ingenuity in tackling the challenges posed by demanding industrial landscapes.