In the realm of modern machinery, the oil seal in a motor is often an unsung hero, playing a critical yet understated role in ensuring smooth operations. For those involved in the maintenance and operation of motors, understanding the intricacies of oil seals can provide immeasurable benefits. Here, we delve into their importance, functionality, and the intricate design that makes them indispensable.

Oil seals, often referred to as grease, fluid, or dirt seals, are essential components designed to protect shafts and bearings from contamination and leakage. Their primary function is to prevent lubricants from escaping the bearings or a specific area of the motor, while also keeping dirt, debris, and moisture from seeping in and causing potential damage. The precision with which these seals operate is a testament to advanced engineering and profound expertise.
At the heart of their design, oil seals typically consist of a rubber-coated metal ring, a flexible lip, and sometimes a garter spring to ensure that the seal grips the rotating shaft firmly. This complex structure allows oil seals to accommodate minor misalignments and maintain a consistent barrier against contaminants. Engineers meticulously select materials for these seals based on the specific requirements of the motor environment, considering factors such as temperature, pressure, and exposure to chemicals. This tailored approach ensures that each oil seal not only fits perfectly but also functions optimally in its specific setting.
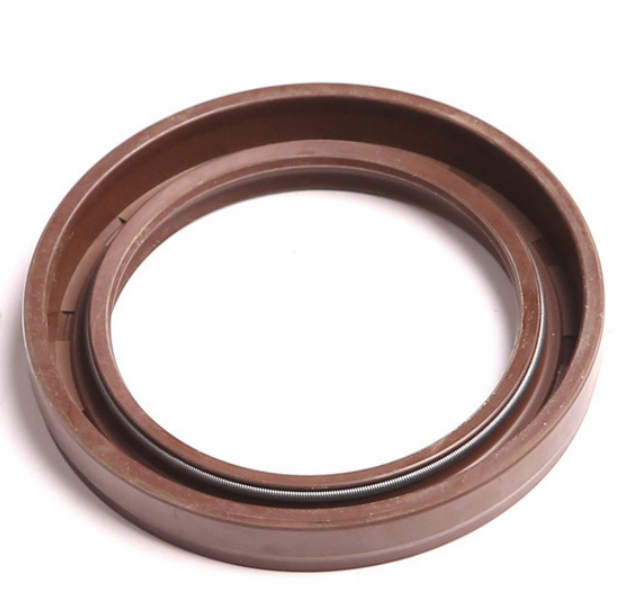
From an experiential standpoint, the incorporation of a well-designed oil seal becomes evident in the longevity and efficiency of the motor. Experienced technicians, who have observed motors over extended periods, often note a significant reduction in maintenance needs when high-quality oil seals are utilized. The prevention of oil leaks not only maintains lubrication at optimal levels but also curbs unnecessary wear on mechanical parts, thereby extending the overall life span of the equipment. The real-world experiences of minimized downtime and enhanced performance highlight the crucial role that these small components play.
oil seal in motor
Authoritative voices in the field, such as leading automotive engineers and industrial maintenance experts, consistently affirm the significance of selecting the appropriate oil seal. Their insights serve as a guiding light, stressing the importance of matching seal material and design to the operational conditions encountered. Moreover, industry standards and guidelines, such as those set by the American Society for Testing and Materials (ASTM), provide a robust framework for ensuring the quality and reliability of oil seals used in motors.
The trustworthiness of oil seals comes from both rigorous testing and decades of field application.
Many oil seals undergo extensive trials to ensure they meet or exceed industry standards. These tests evaluate the seals' ability to withstand varying pressures, temperatures, and chemical exposures over prolonged periods. Testimonials from trustful sources in the industry add layers of assurance, offering firsthand accounts of how superior oil seals have saved time and resources.
Despite their minimal size and cost relative to the entire motor, neglecting the oil seal in maintenance routines can lead to catastrophic failures. Therefore, investing in high-quality oil seals is not merely a matter of purchasing a component but an investment in the reliability and efficiency of the machinery. For industries reliant on motors—from automotive manufacturing to heavy machinery—understanding the indispensable role of oil seals translates directly to enhanced productivity and reduced operational risks.
In conclusion, the oil seal in a motor embodies a combination of technical wisdom, practical experience, and trust. Its presence might be subtle, but its impact on function and reliability is profound and far-reaching. By prioritizing the selection of the right oil seal, industries can ensure optimal performance and longevity of their motors, preventing unnecessary challenges and maximizing their operational capabilities.