In the intricate machinery of modern industry, oil seals play a crucial role in ensuring efficiency and longevity. Designed to retain lubrication and exclude contaminants, these components are vital across numerous sectors, from automotive to aerospace. However, the process of selecting an appropriate oil seal manufacturer involves more than just picking a supplier from a directory. It requires a deep understanding of expertise, experience, and manufacturer credibility, ensuring the highest quality product suited to specific needs.
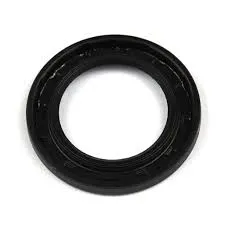
Navigating the world of oil seal manufacturers begins with understanding the production processes and materials used. Reputable manufacturers utilize high-quality materials such as nitrile rubber, silicone, fluorocarbon, and polytetrafluoroethylene (PTFE). Each material offers unique benefits; for example, fluorocarbon provides excellent temperature and chemical resistance, making it ideal for demanding environments. Understanding these nuances reflects the manufacturer's expertise and ability to cater to specific application requirements.
Experience in the field is another critical factor. Established manufacturers with years of experience not only show longevity but a track record of reliability and innovation. They tend to invest in research and development, consistently refining their products to meet industry advancements and regulatory standards. This dedication to continuous improvement is a testament to their commitment to quality and expertise.
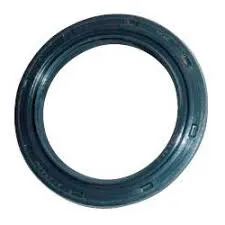
Certifications and industry accreditations further enhance a manufacturer's authoritative standing. Certifications such as ISO 90012015 demonstrate a robust quality management system, ensuring products consistently meet customer and regulatory requirements. Accreditation from industry bodies adds another layer of trustworthiness, showcasing compliance with the highest standards of manufacturing practices.
When it comes to specialized industries, a manufacturer’s capability to customize seals to precise specifications is invaluable. Many manufacturers offer bespoke solutions, working closely with clients to develop seals that address unique operational challenges. Such customization not only highlights the manufacturer's expertise but also their commitment to meeting individual client needs, broadening their appeal across diverse sectors.
oil seal manufacturers
Moreover, the implementation of advanced technology in manufacturing processes is indicative of a manufacturer’s commitment to excellence. Utilization of Computer Numerical Control (CNC) machinery, advanced molding techniques, and quality testing through cutting-edge equipment reflects innovation and precision in production. This technical prowess is crucial for consistently producing high-performance seals that can withstand rigorous operational conditions.
Case studies and testimonials from industry clients often serve as a reflection of a manufacturer's credibility and performance. Positive feedback and successful project outcomes indicate a high level of customer satisfaction. These real-world experiences provide insights into the manufacturer's ability to deliver tailored solutions and maintain strong client relations.
Finally, a manufacturer's support system and aftersales service are integral to building trust. Reliable manufacturers offer comprehensive customer support, including installation guides, troubleshooting assistance, and maintenance advice. This continuous support ensures that clients can rely on their products for long-term performance and dependability.
In conclusion, choosing the right oil seal manufacturer involves a combination of evaluating expertise, experience, and trustworthiness. By focusing on these elements, clients can partner with manufacturers who not only meet their immediate needs but also provide long-lasting, high-quality solutions in the demanding world of industrial machinery.