Oil seal manufacturing plays a pivotal role in maintaining the integrity and efficiency of machinery across various industries. These components are engineered to prevent the leakage of lubricants, as well as ward off the intrusion of contaminants in rotary shafts and stationary applications. Companies that invest in the production of high-quality oil seals demonstrate a superior commitment to precision engineering and quality control.
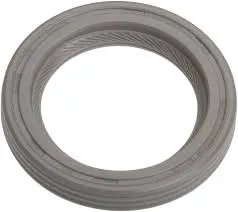
The prowess in oil seal manufacturing begins with understanding the types of seals required for specific applications. Different industries, ranging from automotive to aerospace, rely on oil seals to enhance machine longevity and performance. Manufacturers must possess a wide array of expertise to cater to such varied needs—whether it's crankshaft seals for an internal combustion engine or wheel-end seals for industrial equipment.
Expertise in material science is a crucial component of manufacturing effective oil seals. Selecting the appropriate materials—such as nitrile rubber, silicone, or PTFE—depends on the operational environment and chemical interactions expected during the seal's service life. Using advanced composite materials can further enhance seal performance, offering superior resistance to temperature extremes, chemical exposure, and mechanical stress. This level of expertise assures clients of the durability and reliability of the products they receive.
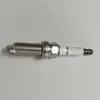
Expert manufacturers employ state-of-the-art technology and rigorous testing protocols to ensure each seal meets stringent industry standards. Utilizing precision CNC machines, manufacturers can produce seals with tolerances measured down to the micron level, ensuring exact fit and performance efficiency. This meticulous attention to detail reflects the manufacturer's authority in the field, as it indicates a robust understanding of the mechanical principles that govern oil seal functionality.
Comprehensive testing and quality assurance processes are at the heart of trustworthy oil seal manufacturing. Reputable manufacturers employ a series of tests, including temperature resistance, pressure testing, and life cycle assessments, to verify that each product can withstand the demands of its intended application. These tests not only validate the performance capabilities of the seals but also build a foundation of trust between the manufacturer and their clientele.
oil seal manufacturing
Manufacturers often collaborate with research institutions to innovate and improve sealing technologies, thereby maintaining their authoritative status. Such partnerships lead to the development of products that push the boundaries of performance and efficiency, keeping the manufacturer at the forefront of the industry. By continually refining their processes and product lines, these companies exemplify a commitment to both innovation and sustainability.
Experience in oil seal manufacturing extends beyond production to encompass customer service and technical support. Leading manufacturers support their clients with comprehensive installation guidelines, maintenance tips, and troubleshooting advice to ensure optimal performance and longevity of the seals. This customer-focused approach builds long-term relationships and positions the manufacturer as an essential partner in their clients' operational success.
Moreover, the adherence to global standards such as ISO certifications and compliance with environmental regulations underscores a manufacturer's dedication to quality and sustainability. These certifications assure clients that the manufacturing process meets internationally recognized benchmarks for safety, quality, and environmental stewardship.
In conclusion, oil seal manufacturing is a complex but critical enterprise that demands a harmonious balance of expertise, authority, and trustworthiness. With a focus on precision engineering, innovative materials, rigorous testing, and customer support, leading manufacturers not only meet but exceed the evolving demands of their diverse clientele. This commitment to excellence fosters a reputation of reliability and industry leadership, ensuring that the machinery around the world continues to operate smoothly and efficiently.