Oil seals, commonly known as rubber parts in the automotive and machinery industries, embody the essence of precision and durability. Crafted meticulously, these components ensure that performance and integrity are maintained in various applications involving rotary and fluid power systems. As industrial and mechanical applications evolve, choosing the right oil seal rubber part becomes a critical endeavor.
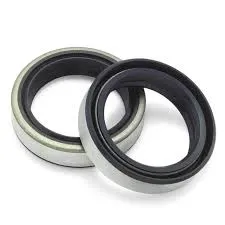
Experienced engineers understand that the performance of machinery is often contingent on the seamless operation of even the smallest components. Oil seals are no exception, given their ubiquitous function in minimizing leakage and protecting against contaminants. These seals not only facilitate smooth mechanical processes but also significantly prolong the life of the system parts they protect. The nuances of oil seal design, material selection, and compatibility with various fluids and temperatures showcase the deep expertise involved in their creation.
In the realm of material expertise, selecting rubber for oil seals introduces benefits that synthetic and other materials may not offer. Natural and synthetic rubbers, such as Nitrile, Silicone, and Viton, are chosen for their distinct properties like elasticity, resilience, and resistance to heat, oil, and assorted chemicals. Nitrile rubber (NBR), for example, is favored for its specialized resistance to petroleum-based oils and fuels. Similarly, Viton seals provide optimal performance at higher temperatures, offering exceptional resistance to chemicals. Such varied applications shed light on the specialized knowledge required to cater to different industrial needs.

Authoritativeness in the realm of oil seal rubber parts underscores the importance of adhering to stringent manufacturing standards and certifications. Leading manufacturers often engage in comprehensive research and development processes to innovate and produce seals that meet global specifications like SAE, DIN, and ISO standards. These certifications not only validate the quality but also ensure compatibility across multiple regions and industries. The collaboration with testing laboratories adds a layer of scrutiny that further affirms a product’s reliability and sets benchmarks for industry standards.
Trustworthiness in choosing high-quality oil seals comes from the reliability and consistency in performance across varied conditions. Real-world testing, coupled with positive client feedback, fosters a sense of reliability among users. For instance, oil seals that consistently demonstrate performance across diverse environments—whether arctic cold or desert heat—are a testament to their engineering excellence and reliability. Testimonials from industry giants using these seals in high-stakes operations often speak volumes about their trustworthiness and effectiveness.
oil seal rubber part
Moreover, the deployment of oil seal rubber parts extends beyond basic functionality. Cutting-edge design features like hydrodynamic lips, which reduce friction and heat generation, and self-lubrication mechanisms that prolong operating life, are now integral to top-tier seals. These innovations ensure efficiency, reduce downtime, and enhance cost-effectiveness, highly-valued features in competitive industrial practices.
Comprehensive knowledge of these seals’ application areas also reinforces expertise. From automotive engines, transmission systems, and power steering to heavy-duty machinery and hydraulic systems, oil seals are pivotal. Each application demands a unique specification of the seal, tailored to withstand pressure, rotational speed, and the presence of diverse fluids. Understanding these intricate requirements further amplifies the expertise of professionals and engineers who implement and design these solutions.
Contributing to sustainability, the production processes of these seals are evolving towards environmentally conscious practices. Recycling initiatives and the development of eco-friendly elastomers represent the industry's commitment to reducing environmental footprints, aligning industrial goals with global sustainability standards. Insights from respected industry analysts and environmental researchers continue to guide these advancements, showcasing a trajectory that balances technology with ecological responsibility.
As advancements continue, the importance of innovation and adaptation in the oil seal rubber parts market remains significant. Embracing new technologies such as artificial intelligence for predictive maintenance and the use of smart materials that adapt to environmental pressures, positions manufacturers at the forefront of modern mechanical engineering.
The multifaceted nature of oil seal rubber parts involves a blend of authentic experience, authoritative knowledge, and a forward-looking perspective on both production and application. As this industry continues to grow, the role of these seals in maintaining operational integrity across global industrial applications is both foundational and transformative.