Oil seals, often overlooked yet crucial components in machinery, play an indispensable role in maintaining the efficacy and longevity of equipment by preventing the leakage of lubricants. Understanding the different types of oil seals is essential for selecting the right one for specific applications, enhancing performance, and reducing maintenance costs. This article delves into the various types of oil seals, offering insight into their applications, advantages, and considerations for optimal use.
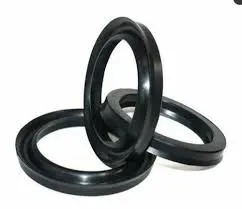
Oil seals, also known as rotary shaft seals, prevent the leakage of oil and grease from machinery, and ensure that harmful contaminants do not enter the system. There are several types, each designed to fit certain requirements based on the operating environment, temperature, pressure, and lubricant used.
1. Single Lip Oil Seals
The single lip oil seal is the most common type, used primarily to retain oil and exclude moderate levels of dirt and debris.
This seal features one flexible lip that maintains tight contact with the shaft. It is best suited for general applications where conditions are not excessively demanding. They are typically made from nitrile rubber, which offers good resistance to oils and fuels, making them ideal for automotive and low-pressure hydraulic applications.
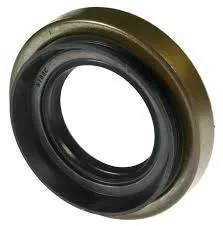
2. Double Lip Oil Seals
Double lip oil seals provide an additional sealing surface, which helps in retaining lubrication while also preventing external contamination. The second lip acts as a dirt exclusion lip, making these seals appropriate for more challenging environments. They are often used in agricultural equipment, wind turbines, and automotive components where exposure to dirt and moisture is significant. Materials like hydrogenated nitrile (HNBR) or fluoroelastomers (FKM) are often chosen for these applications due to their heat resistance and durability.
3. Triple Lip Oil Seals
Designed for extreme conditions, triple lip oil seals feature three lips, further enhancing their capability to seal and protect. These are suitable for off-road vehicles and heavy-duty industrial machinery exposed to harsh environments, including heavy mud, water, and sludge. Typically manufactured using advanced materials such as silicone or FKM, these seals provide enhanced temperature and chemical resistance.
oil seal types
4. PTFE Oil Seals
Polytetrafluoroethylene (PTFE) oil seals are known for their exceptional chemical resistance and ability to function at high speeds and high temperatures. Their low friction characteristic makes them ideal for high-performance applications, such as aerospace and food processing industries. PTFE seals are often used in situations where synthetic lubricants are present and where minimal maintenance is desired.
5. Cassette Seals
These seals are an assembly containing seal lips and other components, forming a complete unit that can be easily installed without damaging the sealing lips. Cassette seals are robust, designed for heavy-duty applications with significant axial movement or misalignment issues. They are predominantly used in wheel-end applications in trucks and buses, benefiting from design features that minimize dirt ingress.
6. Metal-Cased Oil Seals
A metal casing reinforces these seals, enhancing their stability and ease of installation. Ideal for applications with high rotation speed, they provide structural support and precision. Metal-cased seals are frequently employed in mining and construction equipment due to their capacity to handle robust environments.
Key Considerations for Selecting Oil Seals
Choosing the right oil seal involves several considerations to ensure compatibility and performance. Factors such as the operating temperature, shaft speed, pressure, misalignment, and the type of lubricant used should be carefully evaluated. Materials are selected based on environmental conditions—nitrile is suitable for standard conditions, while more demanding settings might require the use of silicone or FKM.
Conclusion
Understanding the different types of oil seals is crucial for achieving the best performance in machinery. Proper selection not only extends the life of the machine but also reduces maintenance time and costs, ensuring long-term operational efficiency. With advancements in materials and design, oil seals continue to evolve, offering more robust solutions for modern engineering challenges. Whether for simple applications or highly demanding environments, there is an oil seal designed to meet specific needs, underscoring its fundamental role in machinery longevity and performance.