Oil seals, also known as rotary shaft seals, play an imperative role in the machinery and automotive industries by preventing leakage and maintaining the correct pressure within systems. With various types available, each suited to specific applications, understanding the differences can greatly enhance performance and longevity of equipment. This exploration will delve into the diverse types of oil seals, emphasizing their unique properties and applications, supported by professional insights and authoritative guidance.

The most commonly recognized oil seal is the lip seal. Typically constructed from a rubber-like material, the lip seal is designed to accommodate a range of temperatures and pressures. Due to its flexible lip that presses against a rotating shaft, it effectively retains lubricating oils, while keeping external contaminants at bay. Suitable for dynamic applications, lip seals are widely used in automotive engines, gearboxes, and pumps. Their versatility and reliability make them an industry staple.
For applications requiring enhanced chemical resistance and temperature tolerance, Teflon seals present a superior alternative. Composed of polytetrafluoroethylene (PTFE), these seals offer reduced friction and a lower coefficient of wear. The unique properties of Teflon make it ideal for seal applications in aerospace, pharmaceutical, and food processing industries where harsh chemicals are prevalent. Additionally, Teflon's non-reactive nature ensures that the quality of sensitive products remains uncompromised.
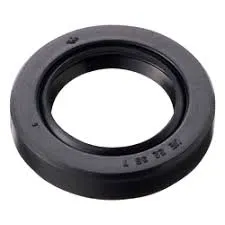
In scenarios where high-speed rotation is a factor, labyrinth seals deliver increased efficacy. Instead of relying on flexible materials, these seals employ a series of intricate pathways that the oil must navigate, effectively using centrifugal force to prevent leakage. Labyrinth seals are prominent in turbo machinery, compressors, and jet engines. Their capacity to function under extreme operational conditions and environments underscores their mechanical robustness.
Mechanical seals distinguish themselves by offering a more advanced sealing solution. Typically comprising two flat faces mounted perpendicular to a rotating shaft, they utilize a precise balance of various forces to maintain an effective seal. Frequently employed in pumps and mixers, mechanical seals afford improved reliability and are capable of managing higher pressures than conventional lip seals. The expertise behind their design minimizes common failure points, thereby extending service life and reducing maintenance demands.
oil seal types
Meanwhile, an emerging innovation in the seal industry is the magnetic fluid seal. This type utilizes a magnetic field to position a ferrofluid in the sealing gap, creating a liquid O-ring effect. Particularly beneficial in applications requiring minimal friction and where any contamination must be avoided, magnetic fluid seals are making significant inroads into the semiconductor manufacturing and optical industries. Their advanced technology ensures ultra-clean sealing without physical contact, which reduces wear and tear.
When selecting an oil seal, key factors such as application environment, operational speed, temperature range, and fluid compatibility must be meticulously considered. Consultation with experts is crucial; a seasoned professional will provide insights into which material and seal type will best suit the specific requirements, thus safeguarding equipment performance and longevity.
Adherence to stringent quality standards is non-negotiable for manufacturers. Reputable brands have established themselves by consistently delivering products that meet or exceed industry norms. Evaluating suppliers based on certifications and customer testimonials can bolster confidence in their offerings.
For maintenance professionals, familiarity with installation procedures and routine inspection guidelines is vital. A properly installed seal significantly reduces the risk of premature failure, while routine checks identify potential issues before they escalate, fostering a preventative maintenance culture.
To summarize, the extensive range of oil seal types available today caters to virtually every conceivable industrial application. Their appropriateness is dictated by not just the mechanical requirements of the equipment but also the operational context. Expertise in selecting the right seal type, backed by authoritative industry recommendations, fosters sustained equipment efficiency and enhances trustworthiness in operational practices. An in-depth understanding of oil seal dynamics empowers businesses to navigate the complexities of mechanical seals, advancing operational integrity and sustainability.