Selecting the right oil seal for a wheel hub is crucial in ensuring the longevity and efficient performance of a vehicle’s wheel assembly. This integral component, though small in size, plays a significant role in maintaining the smooth operation of the wheel by preventing the leakage of lubricants and sealing out contaminants like dirt, dust, and water. For automotive enthusiasts and professionals alike, the understanding and expertise in the selection and maintenance of oil seals can make a marked difference in vehicle maintenance and safety.
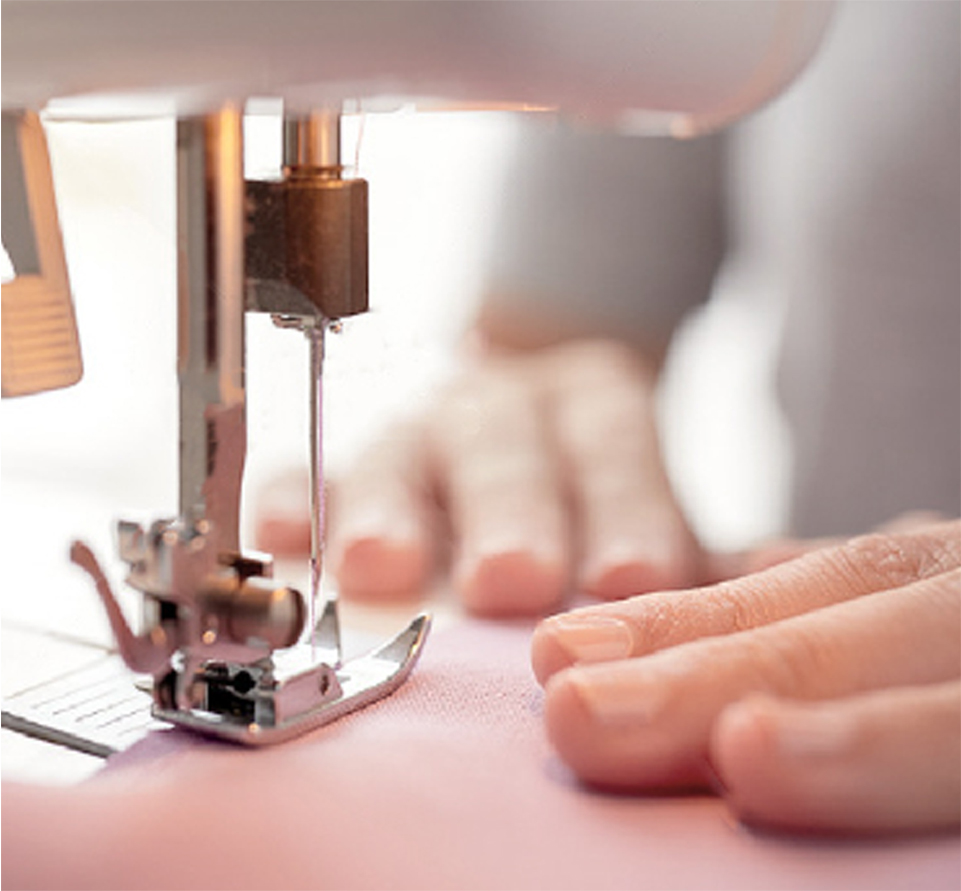
Firstly, it’s essential to comprehend the structure of oil seals. Typically made from materials like rubber, silicone, or PTFE, they are designed to withstand harsh operating environments. The choice of material should align with the specific demands of your vehicle's operating conditions, including temperature ranges, exposure to chemicals, and the type of lubricant utilized. For instance, nitrile rubber is a popular choice due to its excellent resilience against oil, while silicone offers superior temperature resilience for more extreme conditions.
Expertise in oil seal selection starts with an understanding of the wheel hub’s specifications and the operating environment. The professional assessment involves matching the seal to parameters such as shaft diameter, bore size, and width, as well as the pressure that the seal will be subjected to. An expert in automotive components would verify these specifications against the vehicle manufacturer’s guidelines to ensure a perfect fit.
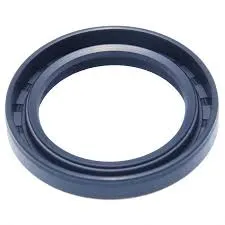
It is also essential to consider the seal's lip design. There are single and double lip seals; choosing the correct one is imperative. Single lip seals are generally suitable for sealing in lubricants, whereas double lip seals provide an additional barrier against external contaminants. Expertise in seal lip technology can significantly enhance the sealing performance, especially in rugged or off-road vehicles where contamination risks are high.
The authority in the market comes from trustworthiness and credible suppliers who ensure their products meet industry standards like ISO 9001 or ISO/TS 16949. This guarantees that the oil seals are manufactured under stringent quality controls. When consulting technical resources or selecting a supplier, relying on those with certifications and positive market reputations can ensure reliability.
oil seal wheel hub
Installation of the oil seal is an area where meticulous care and experience truly matter. A skilled technician knows that improper installation can lead to seal failure despite choosing the right product. Ultimate cleanliness during the fitting process, the proper use of installation tools to avoid nicks or tears, and the attention to lubrication during installation steps amplify the product’s life and performance.
One cannot overlook the importance of routine inspections once the oil seal is operational. Regular checks can help identify potential issues like wear or any seal failure indicators such as lubricant leaks, thus enabling timely interventions and preventing further damage to the wheel hub components.
Innovation in oil seal technology continues to evolve. As an expert staying updated with new materials and designs is vital. Modern seals now come with enhanced features such as low-friction technologies and specialized coatings that extend the service life and improve energy efficiency. Engaging with continuous learning through industry publications or supplier workshops can ensure that you are leveraging the most current advancements in seal technology.
Ultimately, the synergy of experience, expertise, authoritativeness, and trustworthiness in the field of oil seal selection and maintenance for wheel hubs forms the pillar that promotes improved vehicle performance and reliability. By paying heed to the intricate details in selection, sourcing quality products, adhering to precise installation techniques, and maintaining an unwavering commitment to regular inspection and learning, you reinforce the cornerstone of automotive excellence.